|
  |
|
 |
Islamic Textile History : Early Islamic Textiles Images.
Of the many diverse arts that flourished in the early Islamic period, textiles played an especially significant role in society, one that continued in subsequent periods. Textiles were ubiquitous in Islamic lands, serving as clothing, household furnishings, and portable architecture (tents). The manufacture of and trade in textiles were highly sophisticated and profitable industries that built upon Byzantine and Sasanian traditions. Often made with costly materials such as silk and gold- and silver-wrapped thread and decorated with complex designs, textiles were luxury goods signifying wealth and social status.
Islamic textiles were also widely exported to the West, where their prominence is underscored by their impact on European languages. For example, the English words "cotton" and "mohair," and "taffeta" and "seersucker," derive, respectively, from Arabic and Persian. Despite their prevalence, comparatively few textiles have survived from the early Islamic period. Textiles are inherently fragile, and because of their value Islamic fabrics in all periods were cut down and reused over and over again until they literally wore out. Many of the extant early Islamic textiles were found in Egypt, primarily in graves, where the dark and dry conditions helped to preserve them. The fragments that have survived are fabricated from cotton, linen, silk and wool, often dyed vivid colors. They demonstrate a well-developed textile technology notable for its use of complicated and richly colored designs.
One of the most common types of early Islamic textiles is decorated with a long band inscribed with the name and titles of the ruler, as well as the date and place of manufacture. Such inscribed fabrics, of which a number are preserved in the Los Angeles County Museum of Art, are known as Tiraz, from the Persian word "embroidery." As this name suggests, the epigraphic decoration (rendered in Kufic script) was often finely embroidered, but the inscriptions could also be woven directly into the cloth, a technique known as tapestry-weaving.
Other types of early Islamic fabrics were also tapestry-woven, for example a fragment in the museum's collection, whose colorful decoration reflects the influence of Sasanian art. These textiles date from the eighth or ninth century and were likely produced in Egypt, where tapestry-weaving had existed since Pharaonic times. Its linen ground bears a silk decorative band of rather ungainly birds, perhaps ducks, each enclosed by a medallion. The medallions alternate with twin pairs of wings, an abstracted version of the Sasanian royal crown motif. The beaded border usually on the top and bottom is a common means of decoration in early Islamic textiles which was also inspired by Sasanian design. Although the textiles once-brilliant colors have been dimmed by time, and we can now only imagine the larger garment, wall hanging, or cushion they may've once been, it nonetheless enriches our visual perception of early Islamic civilization.
Back to Top
|
|
|
Persian
Silk Textile History: Textile Images
During the 17th century, the Persian aristocracy wore their social status on their sleeves. They were anything but timid about flaunting their rank through the use of rich textiles. They regaled themselves and their horses with these luxurious woven accoutrements and spread them unabashedly on the walls, floors and furniture of their magnificent palaces, even using them to decorate their coffins. In many cases, the textiles were given to royals as tribute.
Persia's shimmering woven silk textiles, often inspired by poems and miniature paintings, exuded a refinement that is a great source of inspiration for design today a sometimes vivid, sometimes pale palette, urbane and understated composition, with cosmopolitan touches imported by way of the merchants of Venice. These gracious courtly works, with their origins based upon naturalistic images of flora and fauna, established the sophisticated design vocabulary of the Safavid empire in its sumptuous textiles as well as its majestic Persian carpets. They are quite a contrast to the geometric abstractions found in a wide range of colorful tribal designs one associates with Persian textiles and rugs woven in the outlying villages.
The history of brocaded silk weaving dates back to the time before the Sassanid dynasty. At that time this handicraft was exported to Europe and Rome. After the Sassanid period, due to the fact that the use of gold was prohibited for men, so weaving of this kind of cloth was almost stopped. During the Mogul era, the textile industry was almost forgotten in Iran, and the masters, for fear of their lives, lived in hiding. The textile industry was revived during the Safavid period, and during the reign of Shah Abbas, brocade artists were asked to migrate to Isfahan, and start working in the royal workshops.
During the period between the 11th and 13th lunar hijira centuries, weaving of brocaded silk declined; and during the Qajar era and the past regime, brocaded silk and velvet were used in formal dresses, upholstery of furniture and curtains of courts. At the present period, some masters such as Mahmoud Farshchian, have put forward novel designs by increasing or decreasing some ornamental elements. Brocades are woven by means of old tools, and its raw materials are silk and gold and silver lace (braid) and are dyed by means of natural stuffs and materials.
In ancient times, ornament making workshops produced valuable textiles for home consumption as well as for exports. Some samples of silk materials from the beginning of the Islamic period and woven in Sassanid style are available now and can be found in private collections and in European churches. For example, the design of the face of Jesus Christ is found in Saint Victoria Church, and the piece of cloth on which the design of elephant is woven, is preserved in "Sceance" Cathedral.
According to historical narrations, two thousand years ago some pieces of cloth were made with gold and silver laces used in their design and fabric. As far as proportionality and coordination of designs and color are concerned, the designs of the Sassanid cloth attained the utmost degree of artistic perfection. The Sassanid designs are mostly birds, animals, hunting ground and horsemen as well as some abstract designs. After the Sassanid period, on account of the fact that men were forbidden to use gold, so, brocades were not made for a relatively long time until the Seljuqi period. During the Islamic period, the brocade and gold designs of animals and birds such as lions, phoenix and eagles made on the fabric of cloth were quite glorious, demonstrating the progress of textile technique during the Seljuqi period. Among the decorative elements of cloth weaving during this period, one could mention the designs of tulips and water lily.
During the succeeding periods, new designs were initiated by designers and textile weavers, which laid the foundation for an independent, genuine and creditable identity of textile of the Safavid period. But before that date that is during the Mogul period the textile was forgotten in Iran for many years, and brocade makers lived in hiding for a long time out of fear of their lives.
The Golden Period for Textiles begins from the Safavid Era.
The silken Safavid pieces of cloth are of three kinds:
1 - Simple fine silk; 2 - Brocade or gold silk; 3 - Silken velvet.
Three pieces of cloth were used for dresses of aristocrats, commanders, kings and courtiers. They were decorated by designs of human beings, animals, birds, flowers and plants as well as scenes of war and feasts. During the period of Shah Abbas, the second, valuable brocade and golden velvet pieces of cloth continued to be woven skillfully and with a great care, which bore the name of the weaver, called "Ghias". There are two small pieces of dated silk cloth from the Shah Abbas era in Metropolitan museum. The name of the weaver, Shah Hossein, and the date 1008 lunar hijira year are inscribed on it. The famous weavers of this era were: Ghias, Abdullah, Bin Mohammad, Moezeddin, Ibne Ghias and Issa Abbasi.
During the Shah Abbas era, some royal workshops were established and brocade artists were asked to migrate to Isfahan and revive this ancient art. Their cooperation showed that the community of brocade makers could produce and market valuable pieces of work. During this period, in addition to Isfahan, Yazd and Kashan were centers of brocade artists in Iran. During the period between 11th and 13th hijira centuries, production of brocade and silk cloth was reduced and was replaced by calico and various kinds of needle lace. Brocades and gold cloth were used mostly by dignitaries and commanders, whereas other kinds of decorative pieces of cloth, such as velvet and satin were worn by men and women. Brocades and golden velvet, in their historical course, attracted the attention of brocade artists during the Qajar period, and this art was retained, more or less, from one generation to another; and in the past regime too, it was used as decorative clothes, upholstery of court's furniture, ceremonial dresses as well as curtains of general or special halls.
Making of Silk in Nature
In Iran, during the spring month of Ardibehest (late April), the process of spinning silk thread starts with silkworm breeders buying boxes of eggs of the silk moth, Bombyx mori (Latin for 'silkworm of the mulberry tree'). They place the eggs in a warm place or in an incubator to help speed the hatching of the eggs, a process that takes about ten days. The eggs will hatch into larvae called silkworms.
At the same time, mulberry trees will have grown new leaves which silkworm breeders buy to feed their silkworm larvae. in Iran, mulberry trees grow in Gilan, Mazandaran, Khorasan, Eastern Azarbaijan, Isfahan, Yazd and Kerman. Once the larvae hatch they eat the leaves of the mulberry continuously.
In Yazd, the town of Taft situated some 18 km southwest of Yazd city is a major silkworm breeding centre.
After the larvae (the silkworm) have moulted four times, that is when they are in the fifth instar, they loose their appetite and are ready to transform themselves into moths. To protect themselves while they are in a vulnerable almost motionless transformational pupa state, they enclose themselves in a protective cocoon enclosure. The cocoon is made out of silk thread, a continuous natural protein filament that they produce in their salivary glands and exude to form the filament.
The larvae's cocoon is built up from about 300 to 900 metres (1,000 to 3,000 feet) of silk filament. The filament is fine, lustrous, and about 10 micrometers (1/2,500th of an inch) in diameter. Each cocoon consists of about a kilometre of silk filament, and about 2,000 to 3,000 cocoons are required to make a pound of silk.
For the making of commercial silk thread, the cocoon's filament is unravelled. The filament from several cocoons are then passed over a pulley, wound together and spun into a thread. Two or three threads are in turn spun together to build a yarn and several strands of yarn can be spun further spun together to make a nett thread. Along the way, the yarn or thread is dyed if needed after which it is ready for weaving
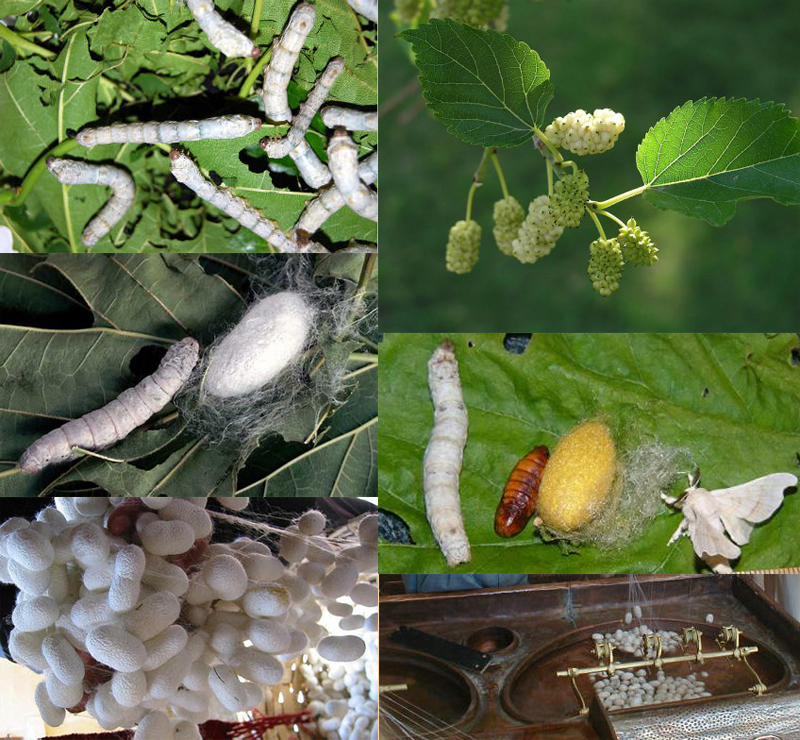
Back to Top
|
|
|
Turkish
Textile History:Textile Images
Textile-weaving traditionally focuses on the making of carpets and kilims as well as other hangings and coverings with names like cicim, zili, and Sumak.
The Turkish arts of textile-making flourished particularly in Anatolia where some of the world's finest textiles were woven in centers such as Konya, Usak, and Bergama during the Seljuk, Feudal, and Ottoman periods. Choice examples of kilims and exquisite textiles are to be found in the Museum of Turkish and Islamic Arts and in the Vakiflar Museum of Carpets and Kilims (both in Istanbul) as well as in a number of other museums in Turkey.
Fabric-weaving is another textile art that has been practiced and developed in Turkey for centuries. Fabrics also provide a medium for the arts of embroidery, hand-painting, and block-printing, as is eloquently testified by examples in museums and private collections around the country. During Ottoman times, cities such as Bursa, Bilecik, and Uskudar were centers where the worlds finest silks, velvets, cottons, and woolens were woven, which live now in the collection of sultans' garments in the Topkapi Sarayi Museum. There are rich examples of fabrics woven in Bursa to order for the court according to designs executed by the artists of the court studios.
The Ottoman world is probably the best known for its production of sumptuous textiles that were woven with shimmering silk and metallic threads. Exquisitely decorated satins and velvets were cherished by both the Ottomans and the Europeans who considered them luxury items that reflected the majesty of kings and the wealth of their courts. Sewn into garments or used as furnishings, they were displayed in ceremonial functions, preserved as treasuries, given as gifts, and demanded as tribute. Silk has always been an expensive and desirable commodity; it was brought from distant lands and required highly specialized and laborious techniques of processing, spinning, dyeing, and weaving; it feels sensuous against the skin but is very durable and can be woven with the most intricate patterns, rendered in brilliant jewel-like colors. Its trade routes and markets were zealously guarded and fought over, since whoever controlled its commercial activities and industrial centers reaped significant financial benefits.
The Ottoman Empire was strategically located on the path of the east-west silk route bridging Asia and Europe. Silk, transported by caravans from Iran passed through Anatolia as far as Bursa, Where Europeans, mostly Italians, purchased the goods. Bursa was the major center for the international silk trade during the early sixteenth century and provided substantial revenues to the state by customs, taxes and brokerage fees levied from the Iranian and Italian merchants; in addition, it developed its own textile industry. The protection of this lucrative trade was of great interest to the sultans and was in part responsible for the wars with the Safavids throughout the sixteenth century.
Most of the raw silk that arrived in Bursa was sold to Europeans, but some was reserved for domestic use. Although silk began to be produced in Bursa in the second half of the sixteenth century, its output was insufficient to supply the demand, and the Ottoman world continued to rely on imported raw material both for its domestic needs and resale.
Back to Top
|
|
|
Chinese Textile History: Textile Images
The earliest known silk textiles excavated in China dated to circa 3630 BCE; earlier pseudo morphs (impressions left by a textile on bronze or jade) or patterned textiles date from the Shang dynasty (16th-11th century BCE). By the Warring States through Han Dynasty periods (circa 475 BCE-220 CE), elaborately patterned jin brocades (1), complex gauze weaves, and intricately embroidered textiles were all being produced; their artistry and technical accomplishment amaze modern viewers.
Trade along the Silk Road, which began as early as the Han dynasty and reached its peak in the 5th through 12th centuries CE, created an environment in which Chinese culture interacted with the tastes of consumers from lands as distant as Iran and Rome. Weavers from a number of ethnic backgrounds, including Han Chinese and Central Asian (Uighur, Sogdian, and others) all produced textiles in different styles woven from silk. Formerly nomadic ruling dynasties, such as the Liao (907-1125), incorporated imagery of hunting and nature into gorgeous gold-brocaded textiles. Kesi (silk tapestry weave) became the vehicle for quintessentially Chinese aesthetics during the Song Dynasty (960-1279) in textiles which feature traditional phoenix and peony motifs or which emulate styles of Chinese brush painting (3). During the Ming (1368-1644) and Qing (1644-1911) dynasties, court robes, rank badges, and Buddhist and Daoist Kesi were all used to denote status and wealth, as well as to express religious devotion.
Typical of Chinese courtly garments are the large, standing dragons, their paws clutching clouds that emblazon most of an Imperial family's clothes. The dragons clutch the jewels they usually pursue; sometimes they are surrounded both front and back with large, gold-couched characters, some of them reading shou (long life). Others are adorned with the swastikas, which mean 'ten thousand,' and combine to form a popular birthday wish for longevity. This symbolism indicates these kinds of garments were intended for such an occasion like a birthday. The color red was very popular and became the Ming dynastic color, which has suggested the owner of these garments would be a woman of the imperial family.
Silk-Knit Goods
Fabrics made of silk consist of many types: brocade, satin, silk fabric, etc. This variety is due to different weaving skills and silk fabrics. Some are lined, some are unbleached, some are heavy, and some are thin. Silk-knit goods are one of great Chinese contributions to the world culture. The weaving skills emerged in the primitive society. They can demonstrate the culture tradition of one nation. Though they historically served as clothing material, its relation to the common people had never been severed. Many excellent weaving skills and patterns were first established by the common people and passed to all walks of life.
Sichuan Brocade
It is one of historical silk-knit brocade and a general term for the silk-knit brocades which were in produced in Chengdu, Sichuan Province, from the Han Dynasty to the Three Kingdom Period. Since Sichuan and the middle China was linked up, the weaving industry has boomed. The varieties, colors, and patterns have become abundant. It flourished until the Tang, Song and Yuan Dynasties. Of the Sichuan brocades in the Tang Dynasty, the bundle flower lining brocade and the red lion and phoenix lining brocade were the most outstanding. Sichuan brocade is based on horizontally colored line.
Cloud Brocade
It is one of the traditional silk-knit brocade. It is named after its color as gorgeous as colorful cloud, for it is made of high quality silk and woven with exquisite skill. The silk industry consists of two trades: the pattern brocade trade and the unpatterned brocade trade since the end of the Qing Dynasty. Not until then the name "cloud brocade" came into use.
Suzhou Brocade
It is traditional silk-knit brocade in Suzhou, Jiangsu Province. It was lost at the end of the Ming Dynasty, and recovered at the beginning of the Qing Dynasty. It consists of big brocade and small brocade. Among them the big brocade is also called heavy brocade, which is mainly used for mounting picture and decoration, while small brocade is used for making box and decorating small articles. They are patterned geometrically and neatly decorated with bundles of flowers and flowers on twigs. They are colored in harmony instead of in contrast.
Zhang Down
It is also called "swans down" and one of the traditional silk -knit goods. It is produced in Zhengzhou, Fujian Province. It flourished in the Ming and Qing Dynasties. There are patterned down and unpatterned down. The patterned down is cut in accordance to the lines and constitutes patterns with the unsevered line circles. The unpatterned down is covered with down circles on its surface.
Tapestry Brocade
It is a type of silk-knit goods whose patterns are highlighted by the colorful horizontal silk. First the horizontal threads are installed on the common weaving machine. Under the horizontal threads there are colorful picture drafts. The vertical threads with various colors are woven in segment by the small shuttles according to the patterns. The horizontal thread of each color is interwoven with the vertical thread with every other color. This way of weaving is called "interweaving horizontal and vertical threads."
Cotton Textiles
Cotton textiles take cotton as material. In the southwest of China the minority nationalities had cotton textiles early in the Eastern Han Dynasty. They called it "white folded cloth.” In Fujian Province of the Han Dynasty, they grew cotton. In the northwest of China of the Three Kingdom Period they also had cotton textiles. The cotton textiles have been produced in the south of the Changjiang River since the Tang Dynasty, especially since the Yuan Dynasty. In the areas populated by the minor nationalities the cotton used to serve as the material which was made into cotton textiles of various colors called brocades. The term "brocade" here refers to textile fabric and textile variety made with different weaving skills. There are silk- knit goods and cotton goods. Some textiles are woven with the blending of silk and cotton.
China: History of Dress
By John S. Major Chinese clothing changed considerably over the course of some 5,000 years of history, from the Bronze Age into the twentieth century, but also maintained elements of long-term continuity during that span of time. The story of dress in China is a story of wrapped garments in silk, hemp, or cotton, and of superb technical skills in weaving, dyeing, embroidery, and other textile arts as applied to clothing. After the Chinese Revolution of 1911, new styles arose to replace traditions of clothing that seemed inappropriate to the modern era.
Throughout their history, the Chinese used textiles and clothing, along with other cultural markers (such as cuisine and the distinctive Chinese written language) to distinguish themselves from peoples on their frontiers whom they regarded as "uncivilized." The Chinese regarded silk, hemp, and (later) cotton as "civilized" fabrics; they strongly disliked woolen cloth, because it was associated with the woven or felted woolen clothing of animal-herding nomads of the northern steppes.
Essential to the clothed look of all adults was a proper hairdo-the hair grown long and put up in a bun or top-knot, or, for men during China's last imperial dynasty, worn in a braided queue-and some kind of hat or other headgear. The rite of passage of a boy to manhood was the "capping ceremony," described in early ritual texts. No respectable male adult would appear in public without some kind of head covering, whether a soft cloth cap for informal wear, or a stiff, black silk or horsehair hat with "wing" appendages for officials of the civil service. To appear "with hair unbound and with garments that wrap to the left," as Confucius put it, was to behave as an uncivilized person. Agricultural workers of both sexes have traditionally worn broad conical hats woven of bamboo, palm leaves, or other plant materials, in shapes and patterns that reflect local custom and, in some cases, ethnicity of minority populations.
The clothing of members of the elite was distinguished from that of commoners by cut and style as well as by fabric, but the basic garment for all classes and both sexes was a loosely cut robe with sleeves that varied from wide to narrow, worn with the left front panel lapped over the right panel, the whole garment fastened closed with a sash. Details of this garment changed greatly over time, but the basic idea endured. Upper-class men and women wore this garment in a long (ankle-length) version, often with wide, dangling sleeves; men's and women's garments were distinguished by details of cut and decoration. Sometimes a coat or jacket was worn over the robe itself. A variant for upper-class women was a shorter robe with tighter-fitting sleeves, worn over a skirt. Working-class men and women wore a shorter version of the robe-thigh-length or knee-length-with trousers or leggings, or a skirt; members of both sexes wore both skirts and trousers. In cold weather, people of all classes wore padded and quilted clothing of fabrics appropriate to their class. Silk floss-broken and tangled silk fibers left over from processing silk cocoons-made a lightweight, warm padding material for such winter garments.
Men's clothing was often made in solid, dark colors, except for clothing worn at court, which was often brightly ornamented with woven, dyed, or embroidered patterns. Women's clothing was generally more colorful than men's. The well-known "dragon robes" of Chinese emperors and high officials were a relatively late development, confined to the last few centuries of imperial history. With the fall of the last imperial dynasty in 1911, new styles of clothing were adopted, as people struggled to find ways of dressing that would be both "Chinese" and "modern."
Cloth and Clothing in Ancient China
The area that is now called "China" coalesced as a civilization from several centers of Neolithic culture, including among others Liaodong in the northeast; the North China Plain westward to the Wei River Valley; the foothills of Shandong in the east; the lower and middle reaches of the Yangtze River Valley; the Sichuan Basin; and several areas on the southeastern coast. These centers of Neolithic cultures almost certainly represent several distinct ethnolinguistic groups and can readily be differentiated on the basis of material culture. On the other hand, they were in contact with each other through trade, warfare, and other means, and over the long run all of them were subsumed into the political and cultural entity of China. Thus the term "ancient China" is a phrase of convenience that masks significant regional cultural variation. Nevertheless, some generalizations apply.
The domestication of silkworms, the production of silk fiber, and the weaving of silk cloth go back to at least the third millennium B.C.E. in northern China, and possibly even earlier in the Yangtze River Valley. Archaeological evidence for this survives tombs from that era; pottery objects sometimes preserve the imprint of silk cloth in damp clay, and in some cases layers of corrosion on bronze vessels show clear traces of the silk cloth in which the vessels had been wrapped. Silk was always the preferred fabric of China's elite from ancient times onward. As a proverbial phrase put it, the upper classes wore silk, the lower classes wore hempen cloth (though after about 1200 C.E. cotton became the principal cloth of the masses).
Depictions of clothed humans on bronze and pottery vessels contemporary with the Shang Dynasty (c. 1550-1046 B.C.E.) of the North China Plain show that men and women of the elite ranks of society wore long gowns of patterned cloth. Large bronze statues from the Sanxingdui Culture of Sichuan, dating to the late second millennium B.C.E., show what appears to be brocade or embroidery at the hemlines of the wearer's long gowns. Later depictions of commoners portray them in short jackets and trousers or loincloths for men, and jackets and skirts for women. Soldiers are shown in armored vests worn over long-sleeved jackets, with trousers and boots.
Chinese silk textiles of the later first millennium B.C.E. (the Warring States Period, 481-221 B.C.E.) testify to the possibility of making very colorful and elaborately decorated clothing at the time. Surviving textiles also demonstrate the widespread appeal of Chinese silk in other parts of Asia. Examples of cloth woven in the Yangtze River Valley during the Warring States Period have been discovered in archaeological sites as far away as Turkestan and southern Siberia. Painted wooden figurines found in tombs from the state of Chu, in the Yangtze River Valley, depict men and women in long gowns of white silk patterned with swirling figural motifs in red, brown, blue, and other colors; the gowns are cut in such a way that the left panel wraps over the right one in a spiral that goes completely around the body. The gowns of the women are closed with broad sashes in contrasting colors, while the men wear narrower sashes. Bronze sash-hooks are common in tombs from the second half of the first millennium B.C.E., showing that the style of narrow waist sashes lasted for a long time. Elite burials also demonstrate a long-enduring custom of the wearing of jade necklaces and other jewelry.
The Han Dynasty
Under the Qin (221-206 B.C.E.) and the Han (206 B.C.E.-7 C.E.; restored 25-220 C.E.), dynasties, China was unified under imperial rule for the first time, expanding to incorporate much of the territory within China's boundaries today. The famous underground terra-cotta army of the First Emperor of Qin gives vivid evidence of the clothing of soldiers and officers, again showing the basic theme of long gowns for elites, shorter jackets for commoners. One sees also that all of the soldiers are shown with elaborately dressed hair, worn with headgear ranging from simple head cloths to formal official caps. Cavalry warfare was of increasing significance in China during the Qin and Han periods; in funerary statuettes and murals, riders are often shown wearing long-sleeved, hip-length jackets and padded trousers.
The well-preserved tomb of the Lady of Dai at Mawangdui, near Changsha (Hunan Province, in south-central China) has yielded hundreds of silk dress items and textiles, from spiral-wrapped or right-side-fastening gowns, to mittens, socks, slippers, wrapped skirts, and other garments, and bolts of uncut and unsewn silk. The textiles show a great range of dyed colors and weaving and decorating techniques, including tabby, twill, brocade, gauze, damask, and embroidery. Textual evidence from the Han period shows that government authorities attempted through sumptuary laws to restrict the use of such textiles to members of the elite landowning class, but that townsmen including merchants and artisans were finding ways to acquire and wear them also.
The period 220-589 C.E. (that is, from the fall of the Han to the rise of the Sui Dynasty), was one of disunity, when northern China was frequently ruled by dynasties of invaders from the northern frontier, while southern China remained under the control of a series of weak ethnically Chinese rulers. Depictions of dress from northern China thus show a predominance of styles suitable for horse-riding peoples. Elite men are sometimes shown wearing thigh-length wrapped jackets over skirts or voluminous skirtlike trousers. In southern China the traditions of colorful Yangtze River Valley silks predominated (though with a discernible trend toward plainer everyday clothing for elite men). Buddhism arrived in China via Central Asia during the late Han period, prompting the production of typical patchwork Buddhist monks' robes, as well as more formal embroidered or appliqué ecclesiastical garments.
The Tang Dynasty
Under the Sui (589-618) and Tang (618-907) dynasties, China was reunified and entered upon a period of unprecedented wealth and cultural brilliance. The capital city of Chang'an (now Xi'an) was, during the eighth century, the largest and most cosmopolitan city in the world. It supported a true fashion system, comparable to that of the modern West, in which rapidly-changing prevailing modes were adopted by fashion leaders and widely disseminated by emulation. Hairstyles (including the use of elaborate hairpins and other hair ornaments) and makeup also changed rapidly in fashion-driven patterns. Ceramic statuettes, produced in huge numbers during the Tang for placement in tombs, often depict people in contemporary dress, and thus give direct evidence for the rapid change of fashions at the time.
Under the Tang, trade along the Silk Route between China via Central Asia to the Mediterranean world flourished, and influence from Persian and Turkic culture areas had a strong impact on elite fashions in China. Chinese silk textiles of the Tang period show strong foreign influence, particularly in the use of roundel patterns. Young, upper-class women outraged conservative commentators by wearing "Turkish" hip-length, tight-sleeved jackets with trousers and boots; some women even played polo in such outfits. (Women more commonly went riding in long gowns, wearing wide-brimmed hats with veils to guard against sun and dust.) Another women's ensemble consisting of an empire-waisted dress tied just below the bustline with ribbons, and worn with a very short, tight-sleeved jacket. This style would reappear several times in later ages, notably during the Ming Dynasty (1368-1644); it strongly influenced the development of the Korean national costume, the hanbok.
Dancers at court and in the entertainment districts of the capital and other cities were notable trendsetters. In the early eighth century, the fashionable ideal was for slender women wearing long gowns in soft fabrics that were cut with a pronounced décolletage and very wide sleeves, or a décolleté knee-length gown worn over a skirt; by mid century, the ideal had changed to favor distinctly plump women wearing empire-line gowns over which a shawl-like jacket in a contrasting color was worn. One remarkable later Tang fashion was for so-called "fairy dresses," which had sleeves cut to trail far beyond the wearer's hands, stiffened, wing-like appendages at the shoulders, long aprons trailing from the bustline almost to the floor, and triangular applied decorations on the sleeves and down the sides of the skirt that would flutter with a dancer's every movement. "Sleeve dancing" has remained an important part of Chinese performative dance since Tang times. Near the end of the Tang period, dancers also inspired a fashion for small (or small-looking) feet that led to the later Chinese practice of footbinding.
The Tang Dynasty was an aristocratic society in which military prowess and good horsemanship were admired as male accomplishments. Depictions of foot soldiers and cavalrymen in scale armor and heavily padded jackets, and officers in elaborate breastplates and surcoats, are common in Tang sculptural and pictorial art.
The Song and Yuan Dynasties
In the Song Dynasty (960-1279), influenced by an increasingly conservative Confucian ideology and social changes that saw the gradual replacement of a basically aristocratic society by one dominated by a class of scholar-gentry officeholders, clothing for both men and women at the elite level tended to become looser, more flowing, and more modest than the styles of the Tang. Women, who sometimes had bound feet, stayed home more, and sometimes wore broad hats and veils for excursions outside the home.
Portraits of emperors and high-court officials during the Song period show the first use of plain, round-necked robes worn either by themselves or as over-robes above more colorful clothing, and also the first appearance of the "dragon robes" embroidered with roundel figures of dragons as emblems of imperial authority.
The Yuan Dynasty (1279-1368) was the Chinese manifestation of the Mongol Empire conquered by Genghis Khan and ruled by his descendants. Mongol men in China, as well as men of Chinese ethnicity, wore loose robes similar to those of the Song period; horsemen wore shorter robes, trousers, and sturdy boots. Round, helmet-like hats were adopted for official use, replacing the earlier black horsehair or stiffened silk official cap. Women of the Yuan period sometimes wore two or more gowns at once, cut so as to show successive layers of cloth in harmonizing colors at the collars and sleeve-openings; Mongol women also wore high, elaborate headdresses like those of the Mongols' traditional homeland.
The Ming and Qing Dynasties
In Ming (1368-1644) times, both men and women wore voluminous clothing, a long robe with wide sleeves for men, a shorter robe worn over a wide skirt for women. In the early and middle Ming, there was a revival of the Tang style of empire-line dresses worn with short jackets, especially for young women. For much of its nearly three centuries of existence, the Ming was a time of prosperity and expanding production of goods of all kinds; there was a concomitant expansion of the type and variety of clothing available to all but the poorest members of society. Cotton, which had been introduced into China during the Song Dynasty, began to be raised extensively in several parts of the country. A short indigo-dyed cotton jacket worn over similar calf-length trousers (for men) or a skirt (for women) became and remained the characteristic dress of Chinese peasants and workers. Cotton batting substituted, in cheaper clothing, for silk floss in padded winter garments.
The dragon robe was adopted for standard court wear for emperors, members of the imperial clan, and high officials. The dragon robe evolved a standard vocabulary of motifs and symbols; typically such a robe was embroidered with large dragons, coiling in space and with the head shown frontally, on the chest and back; smaller dragon roundels on the shoulders and on the skirt of the robe; the space around the dragons embroidered with other auspicious symbols, and the bottom hem showing ocean waves and the peak of Mt. Kunlun, the mountain at the center of the world. The background color of the robe indicated rank and lineage, with bright yellow limited to use by the emperor himself. Official court robes for women were similar but decorated with phoenixes (mythical birds depicted as similar to pheasants or peacocks), the feminine yin to the male yang of the dragon. (Hangings, banners, and other decorative items showing both a dragon and a phoenix are wedding emblems.)
Associated with the dragon robe and the codification of court attire was the use of so-called "Mandarin squares," embroidered squares of cloth that were worn as badges of office for civil and military officials. These indicated rank in the official hierarchy by a set of sixteen animal or bird emblems-for example, a leopard for a military official of the third rank, a silver pheasant for a civil official of the fifth rank. These embroidered squares were made in pairs to be worn on the back and front of an official's plain over-robe, the front square split vertically to accommodate the robe's front-opening design.
The Qing Dynasty (1644-1911) brought new rulers to China-Manchus from the northeast, who overthrew the Ming Dynasty and preserved their hold on imperial power in part by being careful to preserve Manchu dress and other customs in order to keep the small population of conquerors from being submerged culturally by the much more numerous Chinese. The Manchus introduced new styles of clothing for official use; men were to wear short robes with trousers or wide skirts, cut more closely to the body than the flowing Ming styles, fastening at the right shoulder and with a high slit in front to accommodate horse-riding. A distinctive feature of the Manchu robe was its "horseshoe sleeves," designed to cover and protect the back of a rider's hands. Other Manchu styles were the "banner robe" (qipao), a straight-cut long robe worn by Manchu troops, and the "long gown" (chang-shan), a straight, ankle-length garment worn by Manchu women (who wore platform shoes on their unbound feet). Ethnic Chinese women wore loose-fitting jackets over wide skirts or trousers, often cut short enough to reveal the lavishly embroidered tiny shoes of their bound feet.
At court, the emperor, his kinsmen, and high officials wore dragon robes, the symbolic elements of which had been elaborately codified in the mid-eighteenth century; other officials wore plain robes with Mandarin squares. For all ranks, conical hats with narrow, upturned brims were worn for official occasions; buttons of precious or semiprecious stones at the hat's peak also indicated the wearer's rank.
Throughout China's history, the country's population has included many minority peoples whose language, dress, food, and other aspects of culture have been and remain quite different from those of the Han (Chinese) ethnic majority.
Chinese Dress in the Twentieth Century
After the Nationalist Revolution of 1911, it was widely felt in China that, after a century of foreign intrusion and national decline, the country needed to rid itself of old customs in order to compete with the other nations of the modern world. Thus began a search for new styles of clothing that were both "modern" and "Chinese." The simple adoption of Western clothing was not a popular choice; foreign menswear was associated with Chinese employees of foreign companies, who were derided for being unpatriotic; fashionable Western women's clothing struck many Chinese as both immodest and odd. Loose, baggy Western dresses introduced at some missionary schools in China were modest but unattractive.
Many men continued to wear a form of traditional clothing until the mid-twentieth century-a plain, blue, long gown for scholars and older, urban men, jacket and trousers of indigo-dyed cotton for workers. But among urban elites, there emerged in the 1910s a new outfit, based on Prussian military dress and seen first in China in school and military-cadet uniforms; this had a fitted jacket fastened with buttons in front, decorated with four pockets, and made "Chinese" by the use of a stiff, high "Mandarin" collar, worn over matching trousers. This suit was often made, Western-style, in woolen cloth, the first time that wool had ever been the basis of an important Chinese garment type. This outfit became known as the Sun Yat-sen suit, after the father of the Chinese revolution.
Several proposals for creating a modern women's dress for China met with little enthusiasm, but in China's cities, and especially in Shanghai, women and their dressmakers were trying out a modern variation of Manchu dress that was to have lasting consequences. The Manchu "banner robe" (qipao) and "long gown" (changshan, generally known in the West by its Cantonese pronunciation, cheongsam) were adapted by fashionable women to be somewhat more tightly fitting, with a closure folded left-over-right to the shoulder, then down the right seam, often fastened with decorative "frogs" (cloth buttons and loops), and sometimes with a slit to knee height. This new style, in colorful silk, rayon, or printed cotton, was widely publicized in "calendar girl" advertising prints of the 1920s and 1930s, and soon became firmly entrenched as China's appropriately modern women's wear. The qipao (or cheongsam) continued to evolve to become more form fitting, and by the mid-twentieth century was widely accepted, both in China and the West, as China's "traditional" women's dress.
For a few years after the Communist revolution of 1949, older forms of dress, including the man's long "scholar's robe" and the women's qipao, continued to be worn in China. But by the late 1950s, there was strong political and social pressure for people to dress in "modest, revolutionary" styles-the Sun Yat-sen suit (usually in blue cotton, now beginning to be known as a "Mao suit"), or as an alternative, a modest blouse and calf-length skirt. By the time of the Cultural Revolution (1966-1976), the qipao had been denounced as "feudal," and the wearing of the blue Mao suit was nearly obligatory.
Fashion made a cautious return to China in 1978, with the promulgation of the post-Mao "Four Modernizations" program of economic reform. By the early 1980s, fashion magazines had resumed publication, fashion shows were held in major cities, and fashion design and related subjects were beginning to be taught once again at the high school and college level. The qipao also has had a revival, both in China and in overseas Chinese communities, as formal wear that conveys a sense of ethnic pride, and as "traditional" dress worn by women in the hospitality industry. But in general, Chinese dress today is a reflection of global fashion. By the turn of the twenty-first century, prestigious international brands were a common sight in the shopping districts of Shanghai, Guangzhou, Beijing, and other major cities, and Chinese consumers were participating fully in international fashion. Meanwhile China had become the world's largest manufacturer and exporter of garments.
Back to Top
|
|
|
Indian Textile History: Textile Images
India has a diverse and rich textile tradition. The origin of Indian textiles can be traced to the Indus valley civilization. The people of this civilization used homespun cotton for weaving their garments. Excavations at Harappa and Mohenjo-Daro, have unearthed household items like needles made of bone and spindles made of wood, amply suggesting that homespun cotton was used to make garments. Fragments of woven cotton have also been found from these sites.
The first literary information about textiles in India can be found in the Rig-Veda, which refers to weaving. The ancient Indian epics-Ramayana and Mahabharata also speak of a variety of fabrics of those times. The Ramayana refers to the rich styles worn by the aristocracy on one hand and the simple clothes worn by the commoners and ascetics. Ample evidence on the ancient textiles of India can also be obtained from the various sculptures belonging to Mauryan and Gupta age as well as from ancient Buddhist scripts and murals (Ajanta caves). Legend has it that when Amrapali, a courtesan from the kingdom of Vaishali met Gautama Buddha, she wore a richly woven semi transparent sari, which speaks volumes of the technical achievement of the ancient Indian weaver.
India had numerous trade links with the outside world and Indian textiles were popular in the ancient world. Indian silk was popular in Rome in the early centuries of the Christian era. Hoards of fragments of cotton material originating from Gujarat have been found in the Egyptian tombs at Fostat, belonging to 5th century A.D. Cotton textiles were also exported to China during the heydays of the silk route.
Silk fabrics from south India were exported to Indonesia during the 13th century. India also exported printed cotton fabrics or chintz, to European countries and the Far East
before the coming of the Europeans to India. The British East India Company also traded in Indian cotton and silk fabrics, which included the famous Dacca muslins. Muslins from Bengal, Bihar and Orissa were also popular abroad.(Muslin-a very thin cotton material) (Chintz-cotton cloth, usually printed with flowery patterns, that has a slightly shiny appearance)
The past traditions of the textile and handlooms can still be seen amongst the motifs, patterns, designs, and the old techniques of weaving, still employed by the weavers.
BROCADES - THE TRADITION OF BRINGING SILK TO LIFE
Brocade weaving, especially with gold and silver, has been an age-old tradition in India. There are two broad classes of brocades. Brocades of pure silk or silk and cotton blends and zari brocades with gold and silver threads. The most important material in brocade weaving is silk. It facilitates lovely weaves, is durable, strong, fine and smooth. There are several varieties of raw silk of which the chief ones used for brocades are Tanduri, Banaka and Mukta. Tanduri is imported from Malda and other places in Bengal. Banaka is thinner and finer variety and is mostly used to weave soft fabrics such as turbans and handkerchiefs. Mukta is a coarse and durable silk used for kimkhabs, as fine silk would not withstand heavy gold patterns.
REFINING SILK FOR BROCADE MAKING
Raw silk is specially treated for brocades. It is first twisted (called 'silk throwing') after which the threads undergo reeling and checking for uniformity and roundness. When the yarn has been processed, it is bleached and "degummed", as raw silk has a gum-like substance (sericin) in its composition. This has to be removed in order to bring out the sheen and softness and to enable penetration of the dye. The task has to be done with great care as the fibers can weaken or get damaged. The silk is boiled in soap water for certain duration and then sent for dying.
IMPORTANCE OF COLOR
Color plays a vital part in weaving brocade. The charm and subtle beauty of the brocade depends upon color synchronization. Colors are surcharged with nuances of mood and poetic association in fabrics and weaving as much as in painting.
Red - the color of love. The three tones of red evoke the three states of love.
Yellow - is the color of versant (spring), of young blossoms, southern winds and swarms of bees.
Nila (indigo) - the color of Lord Krishna who is likened to a rain-filled cloud.
Hari Nila - the color of water in which the sky is reflected.
Gerwa (saffron) - the color of the earth and of the yogi the wandering minstrel, the seer, the poet who renounces the world.
Earlier, vegetable dyes were used during weaving. These produced fast colors, lasted for almost a generation, and remained as beautiful and vivid as ever. Nowadays aniline dyes have gained popularity as they are cheaper, less time-consuming and produce a larger variety of colors.
MAKING NAKSHAS (DESIGNS) ON BROCADES
Making of nakshas (designs) forms an important part of brocade weaving. Banaras is the main center where the nakshabandha (designer) tradition prevails. The skill and imagination of nakshabandha plays a prominent part in making of designs. Designs are associated with legends and symbolism. The most popular motifs are drawn from nature. In Banaras, it is said that nakshabandha families were brought to this country during the reign of Muhammed Tughlak (1325-1350 A.D.). They were supreme masters of the art of tying designs into the loom. Local artisans and weavers learned this art from these great craftsmen. Some of these craftsmen were also great poets-perhaps they wove their poetry into their designs. One such renowned poet was Ghias-I-Naqsband, mentioned in Abul Fazl's 'Ain-I-Akbari'. The nakshas are first worked on paper. This part of the work is called likhai (writing). The nakshabandha then makes a little pattern of it in a framework of cotton threads like a graph. This pattern gives guidance to the working of that design into weaving.
CHANGES IN DESIGNS THROUGH THE CENTURIES
Designs and motifs have undergone changes gradually and imperceptibly. These changes can be traced through paintings made during different periods. Ajanta and Bagh murals show the existence of different techniques of designs and textiles. During the Gupta period (14th century A.D.). Popular designs were formal floral motifs or scrolls entwined with hansas or sinhas -bird and animal depictions. In the 16th century, the old designs were replaced by Persian floral motifs. Akbari paintings show half-blooming flowers, the Jehangir period, full-blown blossom and the Shahjehan period, tiny blossoms with emphasis on the leaves. In the 19th century, with the advent of British rule, there was a drastic change in designs. Some brocades started depicting English wallpaper designs to suit the tastes of the British rulers.
Back to Top
|
|
|
Italian Velvet History: Textile Images
The most fanciful images of the weaver's art across the centuries: upon thrones, altars, in royal bed chambers, bourgeois drawing rooms and the ateliers of great couturiers; it is velvet which has marked entire eras. Guiseppe Verdi demanded only the finest velvets for the outfits for the characters in his operas, and the same was true for Rossini and Donzietti. From Caruso to Galeffi to Giuditta Pasta, one and all lavished maniacal attention to the velvety spectacle of the costumes of their operas. And what shall we say then for the long list designers, from Courreges, Cardin, Rabanne, Marucelli, and De Barentzen?
Velvet, however, has been first and foremost an economic phenomenon, which has generated enormous wealth, enough to pay armies, create banks, and radically shift the array of international economies. A powerful lever in the great trade of the Renaissance, velvet made the fortunes of the bankers and merchants of city-states such as Lucca, Florence, and the maritime republics of Genoa and Venice. For centuries, these cities dominated the textile markets of the entire world, with their velvets influencing the prices of raw materials, commercial treaties, fashions, technology, and new discoveries.
The earliest traces of velvet were lost somewhere on the legendary Silk Road, the great transcontinental caravan route that connected Lo-Yang with the Ch'ang-an through the Taklimakan, the desert without return, all the way to the port cities of the eastern Mediterranean. As to the origins of velvet, scholars from all over the world have discussed and debated for many years. It is now a general belief this fabric, originally made of silk, arrived in Italy for the first time from the Far East, transported by Arab merchants, and was then spread throughout Europe, in turn, by the merchants from Lucca, Venice, Florence, and Genoa.
In Italy, beginning in the twelfth century and continuing through the entire eighteenth century, the largest industry for the production of velvets in the western world was set up. For centuries in Lucca, Siena, Venice, Florence and Genoa supplied the rest of Europe with these valued fabrics, to be used in clothing, wall coverings, upholstery, the trapping of horses, furniture of all sorts, and the interiors of carriages and litters.
Many historians claim that the earliest velvets were woven in Palermo, in imitation of the velvets in the east. The hypothesis that this precious cloth was first woven in Sicily and later spread to the rest of Italy was first put forth by the French Scholar A. Latour. Many other scholars tend to favor the Venetian route, since there is documentation from as early as the ninth to eleventh centuries of intense trade between Venice and the East. However, Arabic is the only language that makes use of the name of a city Kathifet in mentioning velvet. This city may well be the place where this type of cloth was produced for the first time. But on the other hand, in Italy, the fabric takes the name from the characteristic appearance - in Italian, "vello" means fleece, and "velluto", or velvet, means fleecy.
Back to Top
|
|
|
Japanese Textile History Textile Images
Toward the end of the Edo Period, Japan suffered a succession of disastrous harvests, leading to a sharp decline in the demand for luxury fabrics. And when Japan's capital was moved from Kyoto to Tokyo in 1869, Nishijin weaving seemed threatened with extinction. While these events certainly enfeebled the weaving industry, not to mention the entire Kyoto economy, the Nishijin weavers showed an amazing resilience and spirit in preserving their craft. Observers were sent to Europe to study the textile industry there, and advanced Western weaving technology and equipment were introduced.
By the 1890's, only 20 years after the shift of the capital, the Nishijin weavers had fully adapted modern technology to their ancient art, and the industry began to grow again, along with Japan's new capitalist economy. Through adopting modern technology, the Nishijin weavers were able to create a stable business in inexpensive machine-woven fabrics for everyday use that supported the production of the elaborate and luxurious hand-woven fabrics that are the purest expression of the Nishijin style.
Textiles provide an interesting and revealing vantage point to look at any society. This is particularly the case with Japanese textiles. Beginning in the early modern era when Japan increased its urbanization, textiles became a badge of social status. Because of their closeness to the human body in clothes and other uses, textiles show by their motif, color and garment shape much about Japan and its culture. In addition, they send messages as to an individual’s age, rank, gender, social, political and religious affiliation. In Japan they also often denoted an individual’s occupation, special function and association with special groups. This is the case throughout Japanese history but is perhaps even more apt during the Edo period which we've mentioned above. Economic, commercial and social conditions created levels of change that made textiles and clothing an even more important form of social identification. Many of the criteria and some of the forms and designs of the eighteenth and nineteenth century can still be seen to this day. For example, a preference for natural materials, a preference for traditional decorating techniques and as if a subtle defiance to the dwindling interest in wearing the kimono – the enduring status of the yukata. Textiles continue to this day to demonstrate their commercial uses of demonstrating shops main activities. This can be seen in the present usage of noren (doorway curtain) and advertising banners.
Many observers believe Tsujigahana textiles are the zenith of the Japanese textile arts. These textiles which were produced between the fourteenth and the early seventeenth century for clothes, banners and other items are examples of the height of creativity and beauty. In one sense Tsujigahana textile can be seen as a reflection of Japanese historical changes. Many of the best pieces of Tsujigahana reflect the decorative extravagance of the later Edo period. This coming/lingering of very different artistic sensibilities produced many miracles of artistic and technical brilliance that have not yet been equaled.
Textiles reached a high degree of cultural distinction and artistic appreciation in the Edo and succeeding Meiji periods (1868 - 1912). The social and commercial importance of their role in turn instilled vigor and a greater range of artistic expression. With ties to religion, peasant life and in part as a reaction to a growingly complex urban culture, Japan's textile traditions evolved from commoner textile traditions that had been utilized for centuries. Away from the palace workshops, weavers, dyers and neeedleworkers added to local traditions by adapting foreign techniques, revitalizing patterns by absorbing exotic motifs and creating innovative design.
During the Edo and Meiji periods, elite classes commissioned complicated and diverse fabrics in rich silk brocades and filmy gauze weaves. The lower classes, working within the strictly regulated feudal guidelines for clothing material, patterns and colors were not stagnant during this period. They often created new forms with bold images that were intricate in their subtle nuances. Dyeing emerged as an art form in its own right during this period. Although the use of vibrant colors was often prescribed by the Shogun or economically cost prohibitive, the use of brighter colors increased during this period.
Through the centuries, Japanese textiles have often followed two diverse genuses: the textiles produced for and worn by commoners and those textiles produced for and worn by the higher social classes. Although it might at first be thought that the one could never rival the other in artistic form and creativity, both branches of the textile art are deeply moving embellishments of the country's folk culture.
History of clothing and textiles Textile Images
Ladies making silk, early 12th century painting by Emperor Huizong of Song (a remake of an 8th century original by artist Zhang Xuan), illustrates silk fabric manufacture in China.
Clothing and textiles have been enormously important throughout human history have their materials, production and techniques,cultural influences, and social significance .
Textiles, defined as felt or fibers made into and subsequently netted looped,to make fabrics,appeared in the Middle East during the late From ancient times to the present day, methods of textile production have continually evolved, and the choices of textiles available have influenced how people carried their possessions,clothed themselves,and decorated their surroundings.
Sources available for the study of the history of clothing and textiles include material remains discovered via archaeology; representation of textiles and their manufacture in art; and documents concerning the manufacture, acquisition, use, and trade of fabrics, tools, and finished garments. Scholarship of textile history, especially its earlier stages, is part of material culture studies.
Prehistoric development
A Solutrean needle and fishhook.
Interest in prehistoric developments of textile and clothing manufacture has resulted in a number of scholarly studies since the late twentieth century, including Prehistoric Textiles: The Development of Cloth in the Neolithic and Bronze Ages with Special Reference to the Aegean as well as Women's Work: The First 20,000 Years: Women, Cloth, and Society in Early Times These sources have helped to provide a coherent history of these prehistoric developments. Evidence suggests that human beings may have begun wearing clothing as far back as 100,000 to 500,000 years ago.
Genetic analysis suggests that the human body louse, which lives in clothing, may have diverged from the head louse some 107,000 years ago, evidence that humans began wearing clothing at around this time.
Possible sewing needles have been dated to around 40,000 years ago. The earliest definite examples of needles originate from the Solutrean culture, which existed in France from 19,000 BC to 15,000 BC. The earliest dyed fibers have been found in a cave the Republic of Georgia and date back to 36,000
The earliest evidence of weaving comes from impressions of textiles and basketry and nets on little pieces of hard clay, dating from 27,000 years ago and found in Dolni Vestonice in the Czech Republic.
At a slightly later date (25,000 years) the Venus figurines were depicted with clothing. Those from western Europe were adorned with basket hats or caps, belts worn at the waist, and a strap of cloth that wrapped around the body right above the breast. Eastern European figurines wore belts, hung low on the hips and sometimes string skirts.
Archaeologists have discovered artifacts from the same period that appear to have been used in the textile arts: (5000 BC)
Ancient textiles and clothing
The first actual textile, as opposed to skins sewn together, was probably felt. Surviving examples of Nålebinding, another early textile method, date from 6500 BC. Our knowledge of ancient textiles and clothing has expanded in the recent past thanks to modern technological developments. Our knowledge of cultures varies greatly with the climatic conditions to which archeological deposits are exposed; the Middle East and the arid fringes of China have provided many very early samples in good condition, but the early development of textiles in the Indian subcontinent, sub-Saharan Africa and other moist parts of the world remains unclear. In northern Eurasia can also preserve textiles very well.
Early woven clothing was often made of full loom widths draped, tied, or pinned in place.
Ancient Near East
The earliest known woven textiles of the Near East may be fabrics used to wrap the dead excavated at a Neolithic site in Anatolia, carbonized in a fire and radiocarbon dated to c. 6000 BC. Flax cultivation is evidenced from c. 8000 BC in the Near East, but the breeding of sheep with a wooly fleece rather than hair occurs much later, c.3000 BC in Turkey has also been claimed as the site of the oldest known cloth, a piece of woven linen wrapped around an antler and reported to be from around 7000 BC.
Ancient India
The inhabitants of the Indus Valley Civilization used cotton for clothing as early as the 5th millennium BC – 4th millennium BC. According to The Columbia Encyclopedia, Sixth Edition:
"Cotton has been spun, woven, and dyed since prehistoric times. It clothed the people of ancient India, Egypt, and China. Hundreds of years before the Christian era cotton textiles were woven in India with matchless skill, and their use spread to the Mediterranean countries. In the 1st cent. Arab traders brought fine Muslin and Calico to Italy and Spain. The Moors introduced the cultivation of cotton into Spain in the 9th cent. Fustians and dimities were woven there and in the 14th cent. in Venice and Milan, at first with a linen warp. Little cotton cloth was imported to England before the 15th cent., although small amounts were obtained chiefly for candlewicks. By the 17th cent. the East India Company was bringing rare fabrics from India. Native Americans skillfully spun and wove cotton into fine garments and dyed tapestries. Cotton fabrics found in Peruvian tombs are said to belong to a pre-Inca culture. In color and texture the ancient Peruvian and Mexican textiles resemble those found in Egyptian tombs."
Woven silk textile from tombs at Mawangdui, Changsha, Hunan province, China, from the Western Han Dynasty, 2nd century BC
Evidence exists for production of linen cloth in Ancient Egypt in the Neolithic period, c.5500 BC. Cultivation of domesticated wild flax, probably an import from the Levant, is documented as early as c.6000 BC Other bast fibers including rush, reed, palm, and papyrus were used alone or with linen to make rope and other textiles. Evidence for wool production in Egypt is scanty at this period.
Spinning techniques included the drop spindle, hand-to-hand spinning,and rolling on the thigh; yarn was also spliced. A horizontal ground loom was used prior to the New Kingdom, when a vertical two-beam loom was introduced, probably from Asia.
Linen bandages were used in the burial custom of mummification, and art depicts Egyptian men wearing linen kilts and women in narrow dresses with various forms of shirts and jackets, often of sheer pleated fabric.
Ancient China
The earliest evidence of silk production in China was found at the sites of Yangshao culture in Xia, Shanxi, where a cocoon of bombyx mori, the domesticated silkworm, cut in half by a sharp knife is dated to between 5000 and 3000 BC. Fragments of primitive looms are also seen from the sites of Hemudu culture in Yuyao, Zhejiang, dated to about 4000 BC. Scraps of silk were found in a Liangzhu culture site at Qianshanyang in Huzhou, Zhejiang, dating back to 2700 BC. Other fragments have been recovered from royal tombs in the Shang Dynasty (ca. 1600 BC – c. 1046 BC).
Under the Shang Dynasty, Han Chinese clothing or Hanfu consisted of a yi, a narrow-cuffed, knee-length tunic tied with a sash, and a narrow, ankle-length skirt, called shang, worn with a bixi, a length of fabric that reached the knees. Clothing of the elite was made of silk in vivid primary colours.
Ancient Japan
The earliest evidence of weaving in Japan is associated with the Yayoi period (弥生時代, Yayoi-jidai?) , from about 300 BC to 250.
The textile trade in the ancient world
The exchange of luxury textiles was predominant on the Silk Road, a series of ancient trade and cultural transmission routes that were central to cultural interaction through regions of the Asian continent connecting East and West by linking traders, merchants, pilgrims, monks, soldiers, nomads and urban dwellers from China to the Mediterranean Sea during various periods of time. The trade route was initiated around 114 BC by the Han Dynasty, although earlier trade across the continents had already existed. Geographically, the Silk Road or Silk Route is an interconnected series of ancient trade routes between Chang'an (today's Xi'an) in China, with Asia Minor and the Mediterranean extending over 8,000 km (5,000 miles) on land and sea. Trade on the Silk Road was a significant factor in the development of the great civilizations of China, Egypt, Mesopotamia, Persia, the Indian subcontinent, and Rome, and helped to lay the foundations for the modern world.
Classical antiquity
Greek chiton (left) and chiton worn under himation
Dress in classical antiquity favored wide, unsewn lengths of fabric, pinned and draped to the body in various ways.
Ancient Greek clothing consisted of lengths of wool or linen, generally rectangular and secured at the shoulders with ornamented pins called fibulae and belted with a sash.Typical garments were the peplos, a loose robe worn by women; the chlamys, a cloak worn by men; and the chiton, a tunic worn by both men and women. Men’s chitons hung to the knees, whereas women’s chitons fell to their ankles. A long cloak called a himation was worn over the peplos or chlamys.
The toga of ancient Rome was also an unsewn length of wool cloth, worn by male citizens draped around the body in various fashions, over a simple tunic. Early tunics were two simple rectangles joined at the shoulders and sides; later tunics had sewn sleeves. Women wore the draped stola or an ankle-length tunic, with a shawl like palla as an outer garment. Wool was the preferred fabic, although linen, hemp, and small amounts of expensive imported silk and cotton were also worn.
Iron age Europe
Medieval clothing and textiles
The history of Medieval European clothing and textiles has inspired a good deal of scholarly interest in the twenty-first century. Elisabeth Crowfoot, Frances Pritchard, and Kay Staniland authored Textiles and Clothing: Medieval Finds from Excavations in London, c.1150-c.1450 (Boydell Press, 2001). The topic is also the subject of an annual series Medieval Clothing and Textiles (Boydell Press) edited by Robin Netherton and Professor Gale R. Owen-Crocker of Anglo-Saxon Culture at the University of Manchester.
Byzantium
The Byzantines made and exported very richly patterned cloth, woven and embroidered for the upper classes, and resist-dyed and printed for the lower. By Justinian's time the Roman toga had been replaced by the tunica, or long chiton, for both sexes, over which the upper classes wore various other garments, like a dalmatica dalmatic, a heavier and shorter type of tunica; short and long cloaks were fastened on the right shoulder.
Leggings and hose were often worn, but are not prominent in depictions of the wealthy; they were associated with barbarians, whether European or Persian.
Early medieval Europe
Edgar I of England in short tunic, hose, and cloak, 966
Main articles: "Early medieval European dress"Early_medieval_European_dress">Early medieval European dress, "Anglo-Saxon dress" "/wiki/Anglo-Saxon_dress">Anglo-Saxon dress, and "English Medieval fashion" href="/wiki/English_Medieval_fashion">English Medieval fashion
European dress changed gradually in the years 400 to 1100. People in many countries dressed differently depending on whether they identified with the old Romanised population, or the new Migration period wiki/Migration_period">invading populations such as Franks, Anglo-Saxons, and Visigoths. Men of the invading peoples generally wore short tunics, with belts, and visible trousers, hose or leggings. The Romanised populations, and the Church, remained faithful to the longer tunics of Roman formal costume.
The elite imported silk cloth from the Byzantine, and later Moslem, worlds, and also probably cotton. They also could afford bleached linen and dyed and simply patterned wool woven in Europe itself. But embroidered decoration was probably very widespread, though not usually detectable in art. Lower classes wore local or homespun wool, often undyed, trimmed with bands of decoration, variously embroidery, tablet-woven bands, or colorful borders woven into the fabric in the loom.
High middle ages and the rise of fashion
14th century Italian silk damasks
Clothing in 12th and 13th century Europe remained very simple for both men and women, and quite uniform across the subcontinent. The traditional combination of short tunic with hose for working-class men and long tunic with overgown for women and upper class men remained the norm. Most clothing, especially outside the wealthier classes, remained little changed from three or four centuries earlier.
The 13th century saw great progress in the dyeing and working of wool, which was by far the most important material for outer wear. Linen was increasingly used for clothing that was directly in contact with the skin. Unlike wool, linen could be laundered and bleached in the sun. Cotton, imported raw from Egypt and elsewhere, was used for padding and quilting, and cloths such as buckram and fustian.
Crusaders returning from the Levant brought knowledge of its fine textiles, including light silks, to Western Europe. In Northern Europe, silk was an imported and very expensive luxury. The well-off could afford woven brocades from Italy or even further afield. Fashionable Italian silks of this period featured repeating patterns of roundels and animals, deriving from Ottoman silk-weaving centres in Bursa, and ultimately from Yuan Dynasty China via the Silk Road.
Cultural and costume historians agree that the mid-14th century marks the emergence of recognizable "fashion" in Europe. From this century onwards Western fashion changes at a pace quite unknown to other civilizations, whether ancient or contemporary. In most other cultures only major political changes, such as the Muslim conquest of India, produced radical changes in clothing, and in China, Japan, and the Ottoman Empire fashion changed only slightly over periods of several centuries.
In this period the draped garments and straight seams of previous centuries were replaced by curved seams and the beginnings oftailoring, which allowed clothing to more closely fit the human form, as did the use of lacing and buttons. A fashion for mi-parti or parti-coloured garments made of two contrasting fabrics, one on each side, arose for men in mid-century, and was especially popular at the English court. Sometimes just the hose would be different colours on each leg.
Renaissance and early modern period
Renaissance Europe
Bold floral patterned silks, 15th century.
Main article: 1400-1500 in fashion
Wool remained the most popular fabric for all classes, followed by linen and hemp. Wool fabrics were available in a wide range of qualities, from rough undyed cloth to fine, densebroadcloth with a velvety nap; high-value broadcloth was a backbone of the English economy and was exported throughout Europe. Wool fabrics were dyed in rich colours, notably reds, greens, golds, and blues.
Silk-weaving was well-established around the Mediterranean by the beginning of the 15th century, and figured silks, often silk velvets with silver-gilt , are increasingly seen in Italian dress and in the dress of the wealthy throughout Europe. Stately floral designs featuring a pomegranate or artichoke motif had reached Europe from China in the previous century and became a dominant design in the Ottoman silk-producing cities of IstanbulBursa, and spread to silk weavers in Florence, Genoa, Venice,Valencia and Seville in this period.
As prosperity grew in the 15th century, the urban middle classes, including skilled workers, began to wear more complex clothes that followed, at a distance, the fashions set by the elites. National variations in clothing increased over the century.
Early Modern Europe
Slashing at its height: Henry IV, Duke of Saxony, c. 1514.
Spanish fashion with elaborate reticella ruff, 1609
By the first half of the 16th century, the clothing of the Low Countries, German states, and Scandinavia had developed in a different direction than that of England, France, and Italy, although all absorbed the sobering and formal influence of Spanish dress after the mid-1520s.
Elaborate slashing was popular, especially in Germany. Black was increasingly worn for the most formal occasions. Bobbin lace arose from passementerie in the mid-16th century, probably in Flanders. This century also saw the rise of the ruff, which grew from a mere ruffle at the neckline of the shirt or chemise to immense cartwheel shapes. At their most extravagant, ruffs required wire supports and were made of fine Italian reticella, a cutwork linen lace.
By the turn of the 17th century, a sharp distinction could be seen between the sober fashions favored by Protestants in England and the Netherlands, which still showed heavy Spanish influence, and the light, revealing fashions of the French and Italian courts.
The great flowering of needlelace occurred in this period. Geometric reticella deriving from cutwork was elaborated into true needlelace or punto in aria (called in England "point lace"), which reflected the scrolling floral designs popular for embroidery. Lacemaking centers were established in France to reduce the outflow of cash to Italy.
According to Dr. Wolf D. Fuhrig, "By the second half of the 17th century, Silesia had become an important economic pillar of the Habsburg monarchy, largely on the strength of its textile industry.
During the industrial revolution, production was mechanised with machines powered by waterwheels and steam-engines.
Sewing machines emerged in the nineteenth century.
Synthetic fibers such as nylon were invented during the twentieth century.
Clothing and textile manufacture expanded as an industry so that such unions as the Amalgamated Clothing Workers of America and the Textile Workers Union of America formed early in the twentieth century. Later in the twentieth century, the industry had expanded to such a degree that such educational institutions as UC Davis established a Division of Textiles and Clothing, The University of Nebraska-Lincoln also created a Department of Textiles, Clothing and Design that offers a Masters of Arts in Textile History, and Iowa State University established a Department of Textiles and Clothing that featurs a History of costume collection, 1865–1948. Even high school libraries have collections on the history of clothing and textiles.
Alongside these developments were changes in the types and style of clothing worn by humans. During the 1960s, had a major influence on subsequent developments in the industry.
Textiles were not only made in factories. Before this that they were made in local and national markets. Dramatic change in transportation throughout the nation is one source that encouraged the use of factories. New advances such as steamboats, canals, and railroads lowered shipping costs which caused people to buy cheap goods that were produced in other places instead of more expensive goods that were produced locally. Between 1810 and 1840 the development of a national market prompted manufacturing which tripled the output’s worth. This increase in production created a change in industrial methods, such as the use of factories instead of hand made woven materials that families usually made.
The vast majority of the people that worked in the factories were women. Women went to go work in textile factories because of some of the following reasons. Crowding at home was indeed a cause for them to leave and be on their own. The need to save for future marriage portions also motivated these women to decide to work in the millhouses. The work enabled them to see more of the world, to earn something in anticipation of marriage, and to ease the crowding within the home. They also did it to make money for family back home. The money they sent home was to help out with the trouble some of the farmers were having. They also worked in the millhouses because they could gain a sense of independence and growth as a personal goal. [52]
External links
- Textile production in Europe, 1600–1800
, at the Metropolitan Museum of Art
Things to Wear — A History of Japanese Clothing
Spindle, Loom, and Needle – History of the Textile Industry
Australian Museum of Clothing And Textiles Inc. – Why have a Museum of Clothing and Textiles?
Linking Anthropology and History in Textiles and Clothing Research: The Ethnohistorical Method by Rachel K. Pannabecker – from Clothing and Textiles Research Journal, Vol. 8, No. 3, 14–18 (1990)
The drafting history of the Agreement on Textiles and Clothing
American Women's History: A Research Guide Clothing and Fashion
Historical Clothing/Fabric
History of Clothing Around the World
All Sewn Up: Millinery, Dressmaking, Clothing and Costume
Gallery of English Medieval Clothing from 1906 by Dion Clayton Calthrop
A Short History of Japanese Cotton Textiles
Notes
- Creativity In The Textile Industries: A Story From Pre-History To The 21st Century
- Cambridge History of Western Textiles, p. 1-6.
- Barber 1992; see Bibliography
- Barber 1995; see Bibliography.
- The History of Clothing – How Did Specific Items of Clothing Develop? by Mary Bellis
- Stoneking, Mark. Erratum: Molecular Evolution of Pediculus humanus and the Origin of Clothing".
- Retrieved 2008-03-24. Travis, John.
- The Naked Truth? Lice hint at a recent origin of clothing".
- Retrieved 2007-04-15. Kvavadze E, Bar-Yosef O, Belfer-Cohen A, Boaretto E,Jakeli N, Matskevich Z, Meshveliani T. (2009).30,000-Year-Old Wild Flax Fibers. Science, 325(5946):1359.
- Early History of Textiles & Clothing
- Barber (1994).
- Chang, Gloria. Retrieved 2007-04-15.
- FORENSIC PHOTOGRAPHY BRINGS COLOR BACK TO ANCIENT TEXTILES
- Cambridge History of Western Textiles p. 39-47
- Stein, page 47
- The Columbia Encyclopedia, Sixth Edition. cotton.
- Cambridge History of Western Textiles p. 30-39
- Tang, Chi and Miao, Liangyun, "Zhongguo Sichoushi" ("History of Silks in China").Encyclopedia of China, 1st ed.
- Textile Exhibition: Introduction". Asian art. http://www.asianart.com/textiles/intro.html. Retrieved 2007-08-02.
- (French) Charles Meyer, Des mûriers dans le jardin du mandarin, Historia, no. 648, December 2000.
- Elisseeff, Vadime, The Silk Roads: Highways of Culture and Commerce, UNESCO Publishing / Berghahn Books, 2001,
ISBN 978-92-3-103652-1
- Payne et al.
- Payne 1992, p. 128.
- Piponnier & Mane, p. 114-115
- Owen-Crocker, Gale R., Dress in Anglo-Saxon England, p. 309-315
- Woven into the Earth: Textiles from Norse Greenland
- Françoise Piponnier and Perrine Mane; Dress in the Middle Ages; p. 39; Yale UP, 1997; ISBN 0300069065
- Donald King in Jonathan Alexander & Paul Binski (eds), Age of Chivalry, Art in Plantagenet England, 1200–1400, p 157, Royal Academy/Weidenfeld & Nicholson, London 1987
- Koslin, Désirée, "Value-Added Stuffs and Shifts in Meaning: An Overview and Case-Study of Medieval Textile Paradigms", in Koslin and Snyder, Encountering Medieval Textiles and Dress, p. 237-240
- Laver, James: The Concise History of Costume and Fashion, Abrams, 1979, p. 62
- Fernand Braudel, Civilization and Capitalism, 15th–18th Centuries, Vol 1: The Structures of Everyday Life," p. 317
- "The birth of fashion", in Boucher, François: 20,000 Years of Fashion, Harry Abrams, 1966, p.192
- Fernand Braudel, Civilization and Capitalism, 15th–18th Centuries, Vol 1: The Structures of Everyday Life," p 312-3 and 323 em>
- Singman, Jeffrey L. and Will McLean: Daily Life in Chaucer's England, page 93. Greenwood Press, London, 2005
ISBN 0-313-29375-9
- Black, J. Anderson, and Madge Garland: A History of Fashion, 1975, ISBN 0-6880-2893-4, p.122
- Crowfoot, Elizabeth, Frances Prichard and Kay Staniland, Textiles and Clothing c. 1150 – c. 1450
- Late 15th century Italian (Venice) Velvet at the Metropolitan Museum of Art
- Boucher, François: 20,000 Years of Fashion, Harry Abrams, 1966.
- Boucher, François: 20,000 Years of Fashion, pages 219 and 244
- Montupet, Janine, and Ghislaine Schoeller: Lace: The Elegant Web
- Berry, Robin L.: "Reticella: a walk through the beginnings of Lace" (2004) (PDF)]
- Kliot, Jules and Kaethe: The Needle-Made Lace of Reticella.
- Dr. Wolf D. Fuhrig,"German Silesia: Doomed to Extinction," Heritage: For German-Americans who want to be informedMay 2007): 1.
- Spindel, Loom, and Needle – History of the Textile Industry
- Amalgamated Clothing and Textile Workers Union
- UC Davis Department of Textiles and Clothing History
- University of Nebraska-Lincoln Department of Textiles, Clothing and Design M.A. in Textile History
- Iowa State University College of Family and Consumer Sciences. Department of Textiles and Clothing History of costume collection, 1865–1948, n. d.
- Union-Endicott High School Library Clothing and Textiles – Fashion History
- History of 1960s Fashion and Textiles
- Rorabough, W.J. 1979 The Alcoholic Republic, and American Tradition. New York: Oxford University Press. p.129-131
- Dublin, Thomas. 1994 Transforming Women’s Work: New England Lives in the Industrial Revolution. Ithica, NY: Cornell University Press. p.82
Bibliography
- Alexander, Jonathan, and Paul Binski, eds., Age of Chivalry, Art in Plantagenet England, 1200–1400, Royal Academy/Weidenfeld & Nicholson, London 1987
- Ashelford, Jane: The Art of Dress: Clothing and Society 1500–1914, Abrams, 1996. ISBN 0-8109-6317-5
- Patterns of Fashion: the cut and construction of clothes for men and women 1560–1620, Macmillan 1985. Revised edition 1986. (ISBN 0-89676-083-9)
- Arnold, Janet: Queen Elizabeth's Wardrobe Unlock'd, W S Maney and Son Ltd, Leeds 1988. ISBN 0-901286-20-6
- Barber, E.J.W. (Elizabeth Wayland): Prehistoric Textiles: The Development of Cloth in the Neolithic and Bronze Ages with Special Reference to the Aegean, Princeton University Press, 1992 (Barber 1992)
- Barber, Elizabeth Wayland, Women's Work: The First 20,000 Years: Women, Cloth, and Society in Early Times, W. W. Norton & Company, new edition, 1995 (Barber 1995)
- Robin L.: "Reticella: a walk through the beginnings of Lace" (2004) (PDF)
- Black, J. Anderson and Madge Garland: A History of Fashion, Morrow, 1975. ISBN 0-688-02893-4
- Braudel, Fernand, Civilization and Capitalism, 15th–18th Centuries, Vol 1: The Structures of Everyday Life, p 312-3 and 323, William Collins & Sons, London 1981
- Crowfoot, Elizabeth, Frances Prichard and Kay Staniland, Textiles and Clothing c. 1150 -c. 1450, Museum of London, 1992,ISBN 0-1129-0445-9
- Darwin, George H."Development in Dress", Macmillan's magazine, vol. 26, May to Oct. 1872, pages 410–416
- Elisseeff, Vadime, The Silk Roads: Highways of Culture and Commerce, UNESCO Publishing / Berghahn Books, 2001,ISBN 978-92-3-103652-1
- Favier, Jean, Gold and Spices: The Rise of Commerce in the Middle Ages, London, Holmes and Meier, 1998,ISBN 0841912327
- Gordenker, Emilie E.S.: Van Dyck and the Representation of Dress in Seventeenth-Century Portraiture, Brepols, 2001,ISBN 2-503-50880-4
- Jenkins, David, ed.: The Cambridge History of Western Textiles, Cambridge, UK: Cambridge University Press, 2003,ISBN 0521341078
- Kliot, Jules and Kaethe: The Needle-Made Lace of Reticella, Lacis Publications, Berkeley, CA, 1994.ISBN 0-916896-57-9.
- Kõhler, Carl: A History of Costume, Dover Publications reprint, 1963, from 1928 Harrap translation from the German,ISBN 0-4862-1030-8
- Koslin, Désirée and Janet E. Snyder, eds.: Encountering Medieval Textiles and Dress: Objects, texts, and Images, Macmillan, 2002, ISBN 0-3122-9377-1
- Laver, James: The Concise History of Costume and Fashion, Abrams, 1979*Lefébure, Ernest: Embroidery and Lace: Their Manufacture and History from the Remotest Antiquity to the Present Day, London, H. Grevel and Co., 1888, ed. by Alan S. Cole, at Online Books , retrieved October 14, 2007
- Montupet, Janine, and Ghislaine Schoeller: Lace: The Elegant Web, ISBN 0-8109-3553-8
- Netherton, Robin, and Gale R. Owen-Crocker, editors, Medieval Clothing and Textiles, Volume 1, Woodbridge, Suffolk, UK, and Rochester, NY, the Boydell Press, 2005, ISBN 1843831236
- Netherton, Robin, and Gale R. Owen-Crocker, editors, Medieval Clothing and Textiles, Volume 2, Woodbridge, Suffolk, UK, and Rochester, NY, the Boydell Press, 2006, ISBN 1843832038
- Netherton, Robin, and Gale R. Owen-Crocker, editors, Medieval Clothing and Textiles, Volume 3, Woodbridge, Suffolk, UK, and Rochester, NY, the Boydell Press 2007, ISBN 9781843832911
- Østergård, Else, Woven into the Earth: Textiles from Norse Greenland, Aarhus University Press, 2004,ISBN 8772889357
- Owen-Crocker, Gale R., Dress in Anglo-Saxon England, revised edition, Boydell Press, 2004,ISBN 1-8438-3081-7
- Payne, Blanche: History of Costume from the Ancient Egyptians to the Twentieth Century, Harper & Row, 1965. No ISBN for this edition; ASIN B0006BMNFS
- Payne, Blanche; Winakor, Geitel; Farrell-Beck Jane: The History of Costume, from the Ancient Mesopotamia to the Twentieth Century, 2nd Edn, p1 28, HarperCollins, 1992. ISBN0060471417
- Piponnier, Françoise, and Perrine Mane; Dress in the Middle Ages; Yale UP; 1997;ISBN 0300069065
-
This article is about textile weaving.
Warp and weft in plain weaving
Weaving is a textile craft in which two distinct sets of yarns or threads, called the warp and the filling or weft (older woof), are interlaced to form a fabric or cloth. The warp threads run lengthways on the piece of cloth, and the weft runs across from side to side, across the bolt of cloth.
Cloth is woven on a loom, a device that holds the warp threads in place while filling threads are woven through them. Weft is an old English word meaning "that which is woven".
The way the warp and filling threads interlace with each other is called the weave. The majority of woven products are created with one of three basic weaves: plain weave, satin weave, or twill.
Woven cloth can be plain (in one colour or a simple pattern), or can be woven in decorative or artistic designs, including tapestries. Fabric in which the warp and/or weft is tie-dyed before weaving is called ikat.
The ancient craft of handweaving, along with hand spinning, remains a popular craft. The majority of commercial fabrics in the West are woven on computer-controlled Jacquard looms. In the past, simpler fabrics were woven on dobby looms, while the Jacquard harness adaptation was reserved for more complex patterns. Some believe the efficiency of the Jacquard loom, with its Jacquard weaving process, makes it more economical for mills to use them to weave all of their fabrics, regardless of the complexity of the design.
Process
An Indian weaver preparing his warp
A woman weaving with a manual loom
In general, weaving involves the interlacing of two sets of threads at right anglesto each other: the warp and the weft. The warp are held taut and in parallel order, typically by means of a loom, though some forms of weaving may use other methods. The loom is warped (or dressed) with the warp threads passing through heddles on two or more harnesses. The warp threads are moved up or down by the harnesses creating a space called the shed. The weft thread is wound onto spools called bobbins. The bobbins are placed in a shuttle that carries the weft thread through the shed. The raising and lowering sequence of warp threads gives rise to many possible weave structures.
Both warp and weft can be visible in the final product. By spacing the warp more closely, it can completely cover the weft that binds it, giving a warpfaced textile such as rep weave. Conversely, if the warp is spread out, the weft can slide down and completely cover the warp, giving a weftfaced textile, such as a tapestry or a Kilim rug. There are a variety of loom styles for hand weaving and tapestry. In tapestry, the image is created by placing weft only in certain warp areas, rather than across the entire warp width.
Ancient and traditional cultures
Prehistoric woven objects and weaving tools
Women weaving. Detail from an Ancient Greek Attic black-figure epinetron, ca.500 BC, from Athens. Louvre Museum, Paris.
There are some indications that weaving was already known in the Palaeolithic era. An indistinct textile impression has been found at Pavlov , Moravia. Neolithic textiles are well known from finds in pile dwellings in Switzerland. One extant fragment from the Neolithic was found in >Fayum , at a site dated to about 5000 BCE. This fragment is woven at about 12 threads by 9 threads per cm in a plain weave. >Flax was the predominant fibre in Egypt at this time and continued popularity in the Nile Valley , even after wool became the primary fibre used in other cultures around 2000 BCE. Another Ancient Egyptian item, known as the Badari dish, depicts a textile workshop. This item, catalogue number UC9547, is now housed at the Petrie Museum and dates to about 3600 BCE. Enslaved women worked as weavers during the Sumerian Era and then dried them. Next, they beat out the dirt and the wool. The wool was then graded, bleached , and spun into a thread. The spinners pulled out fibers and twisted them together. This was done either by rolling fibers between palms or using a hooked stick. The thread was then placed on a wooden or bone spindle and rotated on a clay whorl , which operated like a flywheel.
The slaves then worked in three-woman teams on looms, where they stretched the threads, after which they passed threads over and under each other at perpendicular angles. The finished cloth was then taken to a fuller.
Easton's Bible Dictionary (1897) points to numerous Biblical references to weaving in ancient times:
Weaving was an art practised in very early times (Ex. 35:35). The Egyptians were specially skilled in it (Isa. 19:9; Ezek. 27:7), and some have regarded them as its inventors.
In the wilderness, the Hebrews practised it (Ex. 26:1, 8; 28:4, 39; Lev. 13:47). It is referred to in subsequent times as specially the women's work (2 Kings 23:7; Prov. 31:13, 24). No mention of the loom is found in Scripture, but we read of the "shuttle" (Job 7:6), "the pin" of the beam (Judg. 16:14), "the web" (13, 14), and "the beam" (1 Sam. 17:7; 2 Sam. 21:19). The rendering, "with pining sickness," in Isa. 38:12 should be, as in the Revised Version , "from the loom," or, as in the margin, "from the thrum." We read also of the "warp" and "woof" (Lev. 13:48, 49, 51–53, 58, 59), but the Revised Version margin has, instead of "warp," "woven or knitted stuff."
American Southwest
Textile weaving, using cotton dyed with pigments, was a dominant craft among pre-contact tribes of the American southwest, including various Pueblo peoples, the Zuni, and the Utetribes. The first Spaniards to visit the region wrote about seeing Navajo blankets. With the introduction of Navajo-Churro sheep, the resulting woolen products have become very well known. By the 1700s the Navajo had begun to import yarn with their favorite color, Bayeta red. Using an upright loom, the Navajos wove blankets and then rugs after the 1880s for trade. Navajo traded for commercial wool, such as Germantown, imported from Pennsylvania. Under the influence of European-American settlers at trading posts, Navajos created new and distinct styles, including "Two Gray Hills" (predominantly black and white, with traditional patterns), "Teec Nos Pos" (colorful, with very extensive patterns), "Ganado" (founded by Don Lorenzo Hubbell, red dominated patterns with black and white, "Crystal" (founded by J. B. Moore), Oriental and Persian styles (almost always with natural dyes), "Wide Ruins," "Chinlee," banded geometric patterns, "Klagetoh," diamond type patterns, "Red Mesa" and bold diamond patterns. Many of these patterns exhibit a fourfold symmetry, which is thought to embody traditional ideas about harmony, or hózhó.
Amazonia
In Native Amazonia, densely woven palm mosquito netting, or tents, were utilized by the Panoans, Tupí, Western Tucano, Yameo, Záparoans, and perhaps by the indigenous peoples of the central Huallaga River basin (Steward 1963:520). Aguaje palm-bast (Mauritia flexuosa, Mauritia minor, or swamp palm) and the frond spears of the Chambira palm Astrocaryum chambira, A.munbaca, A.tucuma, also known as Cumare or Tucum) have been used for centuries by the Urarina of the Peruvian Amazon to make cordage, net-bags hammocks, and to weave fabric. Among the Urarina, the production of woven palm-fiber goods is imbued with varying degrees of an aesthetic attitude, which draws its authentication from referencing the Urarina’s primordial past. Urarina mythology attests to the centrality of weaving and its role in engendering Urarina society. The post-diluvial creation myt accords women’s weaving knowledge a pivotal role in Urarina social reproduction. Even though palm-fiber cloth is regularly removed from circulation through mortuary rites, Urarina palm-fiber wealth is neither completely inalienable, nor fungible since it is a fundamental medium for the expression of labor and exchange. The circulation of palm-fiber wealth stabilizes a host of social relationships, ranging from marriage and fictive kinship (compadrazco, spiritual compeership) to perpetuating relationships with the deceased.
Islamic world
Girls weaving a Persian rug, Hamadan, circa 1922. Note the design templates ( called 'cartoons') at top of loom.
Hand weaving of Persian carpets and kilims has been an important element of the tribal crafts of many of the subregions of modern day Iran. Examples of carpet types are the Lavar Kerman carpet from Kerman and the Seraband rug from Arak.
An important innovation in weaving that was developed in the Muslim worldduring the Islamic Golden Age was the introduction of foot pedals to operate a loom. The first such devices appeared in Syria, Iran and Islamic parts of East Africa, where "the operator sat with his feet in a pit below a fairly low-slung loom." By 1177, it was further developed in Al-Andalus, where having the mechanism was "raised higher above the ground on a more substantial frame." This type of loom spread to the Christian parts of Spain and soon became popular all over medieval Europe.
Europe
Dark Age and Medieval Europe
Weighted-warp looms were commonplace in Europe until the development of more advanced looms around the 10th–11th centuries. Especially in colder climates, where a large floor loom would take up too much valuable floor space, the more primitive looms remained in use until the 20th Century to produce "homespun" cloth for individual family needs. The primary material woven in most of Europe was wool, though linen was also common, and imported silk thread was occasionally made into cloth. Both men and women were weavers, though the task often fell to the wife of a farming household. Fabric width was limited to the reach of the weaver, but was sufficient for the tunic-style garments worn in much of Europe at the time. A plain weave or twill was common, since professional weavers with skills to produce better fabrics were rare.
Weaving was a strictly local enterprise until later in the period, when larger weaving operations sprung up in places like Brugges, in Flanders. Within this setting, master weavers could improve their craft and pass skills along to apprentices. As the Middle Ages progressed, significant trade in fine cloth developed, and loom technology improved to allow very thin threads to be woven. Weaver's guilds (and associated craft guilds, like fullers) gained significant political and economic power in some of the bigger weaving cities.
Colonial America
Colonial America was heavily reliant on Great Britain for manufactured goods of all kinds. British policy was to encourage the production of raw materials in colonies. Weaving was not prohibited, but the export of British wool was. As a result many people wove cloth from locally produced fibers in Colonial America.
In Colonial times the colonists mostly used wool, cotton and flax (linen) for weaving, though hemp fiber could be made into serviceable canvas and heavy cloth also. They could get one cotton crop each fall, but until the invention of the cotton gin it was a labor-intensive process to separate the seeds from the cotton fiber. Flax and hemp were harvested in the summer, and the stalks rendered for the long fibers within. Wool could be sheared up to twice yearly, depending on the breed of sheep.
A plain weave was preferred in Colonial times, and the added skill and time required to make more complex weaves kept them from common use in the average household. Sometimes designs were woven into the fabric but most were added after weaving using wood block prints or embroidery.
Industrial Revolution
Before the Industrial Revolution, weaving remained a manual craft, usually undertaken part-time by family craftspeople. Looms might be broad or narrow; broad looms were those too wide for the weaver to pass the shuttle through the shed, so that the weaver needed an assistant (often an apprentice). This ceased to be necessary after John Kay invented the flying shuttle in 1733, which also sped up the process of weaving.
Great Britain
The first attempt to mechanise weaving was the work of Edmund Cartwrightfrom 1785. He built a factory at Doncaster and obtained a series of patents between 1785 and 1792. In 1788, his brother Major John Cartwight built Revolution Mill at Retford (named for the centenary of the Glorious Revolution. In 1791, he licensed his loom to the Grimshaw brothers of Manchester, but their Knott Mill burnt down the following year (possibly a case of arson). Edmund Cartwight was granted a reward of £10,000 by Parliament for his efforts in 1809. However, success in power-weaving also required improvements by others, including H. Horrocks of Stockport. Only during the two decades after about 1805, did power-weaving take hold. Textile manufacture was one of the leading sectors in the British Industrial Revolution, but weaving was a comparatively late sector to be mechanised. The loom became semi-automatic in 1842 with Kenworthy and Bulloughs Lancashire Loom. The various innovations took weaving from a home-based artisan activity (labour intensive and man-powered) to steam driven factories process. A large metal manufacturing industry grew to produce the looms, firms such as Howard & Bullough of Accrington, and Tweedales and Smalley and Platt Brothers. Most cotton weaving took place in weaving sheds, in small townscircling Greater Manchester and worsted weaving in West Yorkshire– men and women with weaving skills emigrated, and took the knowledge to their new homes in New England, in places like Pawtucket and Lowell.
The invention in France of the Jacquard loom, enabled complicated patterned cloths to be woven, by using punched cards to determine which threads of coloured yarn should appear on the upper side of the cloth.
America,1800–1900
The Jacquard loom attachment was perfected in 1801, and was becoming common in Europe by 1806. It came to the US in the early 1820's, some immigrant weavers bringing jacquard equipment with them, and spread west from New England. At first it was used with traditional human-powered looms. As a practical matter, previous looms were mostly limited to the production of simple geometric patterns. The jacquard allowed individual control of each warp thread, row by row without repeating, so very complex patterns were suddenly feasible. Jacquard woven coverlets (bedspreads) became popular by mid-century, in some cases being custom-woven with the name of the customer embedded in the programmed pattern. Undyed cotton warp was usually combined with dyed wool weft.
Natural dyes were used until just before the American Civil War, when artificial dyes started to come into use,
The weaving of textiles is another of the more ancient crafts of mankind, and another of those essential to a pioneer society. Its origins are lost, along with those of many other crafts, in the deep shadow of Time.
Simple fabrics are made by weaving threads in and out across a layer of other threads at a right angle. An obscurity has fallen over the details of this once common process today when the average person has little or no contact with the means by which his cloth is manufactured. Also, it is a far cry from the miraculous efficiencies of industrial weaving to the simple methods of the hand loom. Yet the mysteries of warp and woof, heddle and shuttle, are not very profound and may be easily understood.
The warp is the lengthwise threads. These must be the strongest and are usually of a better type or grade of thread than the crosswise threads, called the woof, or weft.
A loom is a frame upon which the warp threads are vertically stretched. These threads are passed, at top and bottom, through tiny loops of string or wire on small pieces of wood, called heddles, which resemble minute piano keys. At the top of the loom every other heddle is attached to one crossbar, while the intervening ones are attached to another. Thus, when one crossbar is pushed out every other thread is separated from its neighbor. When the other crossbar is pushed out the action is reversed. In weaving this permits the easy separation of every other warp thread so that the woof thread, attached to a shuttle, has merely to be tossed through the intervening space, after which the separation of the warp threads is reversed and the shuttle is passed back again. The above process is for the weaving of simple, unpatterned textiles. When patterns are desired, more than two sets of heddles are necessary, for threads of different colors. The foot-loom, with various pedals to work the crossbars, thus leaving both hands free to manipulate the shuttle, came in the early 17th or late 16th centuries. To produce still more intricate patterns the draw-loom was invented. This was a method whereby the many sets of heddles were operated by cords which were pulled by a skilful small boy who had to swing about precariously, monkey-fashion, atop the large loom.
In 1733 John Kay, an Englishman, invented the flying shuttle; a means of making the shuttle pass back and forth by the pulling of cords instead of by hand to hand tossing. But this invention did not find ready acceptance.
Then in 1784 Edmund Cartwright invented the power loom, which performed all the operations of moving the heddles and the shuttle in any manner desired. Cartwright was an English clergyman with no knowledge of weaving and practically none of mechanics. He is an outstanding example of the frequency with which amateurs in the crafts and sciences make great discoveries, possibly because they are uninhibited by any knowledge of the "real difficulties" involved in their ideas. The superhuman weaving machinery of today's textile mills is essentially based on the principle of the simple loom of antiquity.
It was really not until almost the 18th century that Great Britain became frightened at the possibility of American manufactures making the Colonies economically independent. The London Company had sent weavers, among innumerable other craftsmen, to Jamestown in 1620. There was no 17th century British resistance to cloth manufacture in New England.
The Pilgrims landed at Plymouth in 1620 and the Puritans came to Massachusetts Bay in 1630, and although their hardships were terrible their success was sufficient to induce large numbers of other persons, mostly with similar religious persuasions, to follow them to New England.
Almost all Colonial families sowed flax and hemp. The "hemp" was not really hemp but a species of bark, Apocynum Cannabinum, used by the American Indians. Although cotton was indigenous to the American continent, the only cotton available to the early American Colonists was imported from the Barbados.
A great deal of weaving was carried on by journeymen. These were travelling craftsmen. Their title, however, does not come from the fact that they travelled but from the fact that originally the term "journey" meant a day's work. In other words, they were craftsmen who worked by the day. They were active not only in weaving, but in a greater or lesser degree, in pottery, carpentry, tailoring, and various other crafts. Sometimes, in the later frontier days, they were on their way to a permanent home. Sometimes they simply liked to travel. They were an enlivening influence throughout the Colonies and were depended upon for vivid gossip and tall tales of other places.
Weaving was, in earliest America, for the most part a household industry. Most housewives could perform its simple operations but it did have a professional craft aspect. There were some families having looms but not knowing how to use them adequately. It was for such as these that the journeymen travelled from home to home, weaving various fabrics.
Puritan Governor Bradford was himself a fustian weaver from Austerfield, England, which probably did a good deal for tolerant laws toward weavers in the Massachusetts Bay Colony. The warp, in those days, could not be made from cotton for the technique of spinning a sufficiently strong cotton thread had not yet been developed. The commonest fabrics of the period were a mixture of linen and cotton which was variously called "fustian," "dimity," etc.
Weavers who established themselves in a fixed locale were accustomed, according to J. L. Bishop in his History of flmerican Manufactures, ". . . to provide themselves with the linen warp and the new cotton each on his own account. It was then carded and spun by their wives and children and afterward woven by the head of the family. The weaver plied his loom during a part of the day, the remainder being employed in gardening or other affairs." The cloth was then carried to the nearest market for sale. During these times when the Colonial government was so concerned about the home manufacture of textiles, bounties were paid for the growing of fibres and for the weaving of fabrics.
The method of non-itinerant weaving, just described, was made tremendously more efficient about 1740 by a completely new system. Textile merchants sent their agents throughout the country to supply household weavers with linen yarn and raw cotton at stated intervals and received their woven cloth in return.
Thus, by approximately 1767, there were three kinds of American textile manufacture. The greatest amount was probably amateur activity. Most early American housewives could weave as well as spin. They wove fabrics for the family needs and sold any excess in the city markets. Second, were the homes that had looms but did not know how, or did not wish to use them. These were serviced by the journeymen weavers who were paid ten to twelve pence for each yard of a half-yard width of material. Third were the non-itinerant weavers, supplied with threads by central distributors, working, in effect, by consignment.
About 1700, when the population of the English Colonies in America had reached 250,000, the British suddenly became aware of the danger of American manufacturing enterprise and began to fight it with intolerable laws. After they had lost the Revolutionary War thus precipitated they continued to struggle in the purely economic field by selling British goods in America for as much as 25% less than the price in London.
When craftsman-inventor Eli Whitney invented his cotton gin in 1783, he influenced the course of American history, for the first three quarters of the 19th century. Before the cotton gin there had been a stronger "abolition" sentiment in the South than in the North, due to the increasing unprofitableness of slaveholding. This vanished with Whitney's invention, for when the negroes could be used for extensive cultivation and picking, their maintenance became practical. Still more important, the slave-owning plantation owners were no longer confined to the Tidewater areas for they could now use the short-fibred upland cotton which had not previously been satisfactory. With this impetus the Southern cotton interests rose rapidly to a national domination and to a conflict with Northern economy which was only terminated, and not altogether justly, by the Civil War.
Eli Whitney's little machine increased cotton production in America one hundred fold in the first seven years of its existence, and made cotton one of the essential determinants of world situations unto this present day.
Silk worms were nurtured in Georgia as early as 1734, but it was not until 1 8 10 that the first American silk mill was successfully operated in Mansfield, Connecticut.
One of the variations on plain weaving in early Colonial times was the making of coach-lace, which was not lace at all but was a woven strip with ornamental braid in floral or geometric patterns.
As in England, the printing of cotton in this country was early inspired by the beauty of India prints. American cotton prints were at first done in simple colors from rectangular wooden blocks on which the design was either raised, or cut intaglio. That some of these blocks were carved by real artists or craftsmen is indicated in the advertisement of Francis Dewing in Boston, 1716, who claimed that he ". . . engraveth and printeth Copper Plates, likewise cuts neatly in wood and Painteth Calicoes." American cotton printers in general imitated the patterns of India Prints, but after the Revolution eagles and other patriotic symbols came into fashion.
In the process of printing the fabric was fastened to the floor or to a large table. The block was "inked" by pressing it onto a color pad, in the manner of a rubber stamp. The block was then applied to the material. For greater "fastness" the dye was sometimes mixed with glue.
Perhaps the greatest of all American non-professional crafts was that of weaving coverlets. Rural women wove these of coarse yarns from early Colonial times far into the 19th century. They are a truly American expression. The patterns, sometimes recorded on paper, were called "drafts" and were passed around from family to family, town to town, county to county. These patterns, like folk-stories and folk-music, were gradually added-to by the more creative persons who used them until they changed beyond recognition. Each had an obscure evolution of its own.
Some of the patterns have commonplace, realistic names, such as "Sunrise," "Cat Tracks," "Dog Tracks," and so on. Others are direct expressions of Americanism, such as the one called "E pluribus unum," and another known as the "Declaration of Independence." This latter one has a formal floral pattern in its central area, but the border is composed of columns, stars, and eagles holding bunches of arrows in both feet, instead of only the left as in the Seal of the United States. Also, on the coverlet, the eagles have the national shield apparently tattooed on their lower bellies instead of being borne on their breasts. On one such cover is woven: "American Independence. Declared July q., 1776. Wove in 1839. J. A. Getty."
Other patriotic "drafts" are George Washington, and Anthony Wayne. Masonic emblems were also common.
But the majority of these coverlet patterns are rather obscure abstractions entitled, variously: Governor's Garden, Rich Man's Fancy, Bonaparte's Retreat, Winding Leaves and Folding Win dows, Queen of England, Youth and Beauty, Muscadine Hulls, Ladies' Delight, Frenchman's Fancy, Tennessee Trouble, and Missouri Trouble.
Next in prominence to the coverlet are the familiar American "samplers." These are embroidered pictures and words done on a background of coarse linen or canvas. Technically speak ing they are not samplers unless they are signed and dated, but are merely embroidered pictures.
In the beginning samplers were highly intricate displays of embroidering virtuosity. It was in the 19th century that they became primers for the female young. One of the earliest and most excellent specimens, still in existence, was made by Miles Standish's daughter, Lora, in 1623.
In the 19th century the sampler had become largely a device for keeping young girls out of trouble! The young ladies were handed squares of linen, needles, and colored threads and directed to work out pictures of animals, houses, and flowers, combined with religious, filial, and moral sentiments. When the family could not think of any pious sentiment the girls were often instructed to embroider the alphabet, which thousands dutifully did, sometimes in both capital and small letters. Maps were occasionally embroidered as an instruction in geography, and in the second quarter of the 19th century there occurred the celebrated morbid era when the deaths of illustrious persons or relatives were the subject of such art work. Tombs and winged angels of death poured from the needles of all the industrious maidens.
The sampler was also used as a genealogical record, in the manner of the Family Bible. Deaths, births, and marriages were recorded in various appropriate colors whenever an occasion arose.
The final addition to the list of characteristic American household textile crafts is the art of richly-colored and varipatterned quilt-making as it has been practiced by rural house wives from earliest times to the present. These manifold aspects of folk-art and handicraft constitute one of the richest seams of our national cultural heritage.
BARCELAND, BARCELONA: A kind of silk handkerchief or neckcloth said to have been made originally at Barcelona, Spain.
BARGELLO-WORK: (Flame-stitch, Hungarian-stitch) Originated in Italy, where it was worked in silks. English work waa carried out in crewels. The figure is usually a series of pointed or flame-like forms.
BAUDEKIN: A rich cloth sometimes mentioned in connection with bed-hangings in the Middle Ages. Now called brocade (q.v.).
BAYEUX TAPESTRY: This is not strictly a tapestry, but a specimen of early medieval embroidery with a border, top and bottom, resembling sampler work, using woolen thread of various colors on a heavy brown linen cloth. It is 214 feet long and 20 inches wide, and is a panorama representing the invasion and conquest of England by William the Conqueror in 1066. It contains the figures of over 600 men, 200 horses, 40 ships and boats, besides numerous birds, animals and other objects in 72 scenes, with Latin inscriptions giving the subjects and names. Tradition asserts it to be the work of Matilda, wife of William, and the women of her household. It is now preserved in the library at Bayeiuc, episcopal city of Normandy.
BAYS, BAYES, BAIZE: A coarse woolen stuff having a long nap used chiefly for linings, curtains, etc., introduced into England from France in the 16th century. In finer texture used for clothing.
BEAUVAIS TAPESTRIES: Beauvais.
BED-HANGINGS: These consisted of tester, celour, curtain and bed-coverings in the Middle Ages. In the 16th century, when the bed took the form of wainscot. head and tester, supported by two posts, the hangings were limited to curtains and valances. Later, the beds were entirely covered and draped in textiles, until in the Georgian period they became again less pronounced. BERLIN WOOL WORK: A type of needlework invented in Berlin, Germany, early in the 19th century, the design being blocked and colored on canvas, and done by the crossstitch. The best Berlin-work was for furniture coverings in flower and conventionalized designs. The so-called zephyr wool, a fine dyed worsted, gave the best results, but silk, chenille and beads were also used. This work was very popular here, also in England, following the decline of the sampler in the Victorian period.
BLEACHING: This is the process of whitening textile fibers and fabrics by exposure to the sun and weather, as it was practised before the Christian era, or by treatment with chemicals. In the 18th century a bleaching solution of potash and lye was used and in 1785 the powerful bleaching quality of chlorine was discovered, since which time various other bleaching processes have been discovered. BOBBIN LACE: The name is derived from the bone bobbin used, in distinction from the needlepoint lace. This form of lace-making was introduced into England in the last half of the 16th century and in the time of Queen Anne had become a prominent industry. It was first made in this country at Ipswich, Massachusetts, in the 18th century by workmen from England. BOMBASINE (also Spelled BOMBAZEEN): A twilled or corded dress material composed of silk and worsted. In black, much used for mourning.
.BROADCLOTH: A fine woolen double-width cloth with a smooth-finished surface.
BROCADE: The term, derived from the Spanish broche, meaning the pointed bobbin of the high-warp loom, originally meant the combination of bobbin and shuttle effects. The pattern is woven over a shuttle fabric during the process of weaving, thus bringing the design into relief. Brocades were used for bedhangings and for the upholstery of chairs in England in the 17th and 18th centuries.
BROCATEL: A coarse brocade of linen, chiefly used for tapestry effects in wall hangings.
BUCKRAM: At first a fine linen or cotton fabric; later, stiffened with gum or paste.
CALICO: A somewhat coarse cotton fabric. It took its name from Calicut, a city on the coast of Malabar, where it was first manufactured. In Colonial times it was imported from England and the prints of Robert Peel of Lancashire were widely worn by the women of this country. PRINTING.
CALIMANCO: A glazed woolen stuff of Flanders woven with satin twill and checkered in the warp, so that the checks are seen on one side only. Much used in the 18th century.
CAMAK Also called Camorca, a fabric of silk and fine camel's hair in use in the 14th and 15th centuries.
CAMBLET: (Or CAMLET) A stuff originally of silk and camel's hair, popular in the 18th century for bed-hangings and upholstery. Later, made of silk and wool.
CAMBRIC: A very fine, thin linen.
CANVAS: Stout, heavy cloth woven in the same way as linen, usually of unbleached cotton or of flax, sometimes of jute. CARDING: The process of cleaning cotton of any foreign substances after "ginning," and to reduce it to a ribbon of thin fleece to be run through the drawing and roving machines into a thread-like form before it is wound on the bobbin.
CARPETS: Carpets probably originated in Persia where they were for centuries handwoven, both as carpets and rugs. The art spread eastward through India and China and westward through Turkey in Asia. Early importations into Europe were from Asia Minor, which gave the name Turkeywork (q.v.) to the product, and those made in England and in France in the 17 th century of hand-knotted pile went by the name of Turkey-work. By the middle of the 18th century the making of pile carpets had become an important English industry. It received a great stimulus by the influx of French Huguenot carpet-weavers. In England, during early times, the word "carpet" was applied to the coverings of beds, tables, cupboards, etc., and the same practice was followed in this country. It was not until the middle of the 18th century that the word was applied to floor coverings. The first factory in this country for the manufacture of yarn carpets was started at Philadelphia, late in the 18th century.
Axminister Carpets. Originally made at Axminster, England. The texture was chenille, soft and very agreeable, resembling Smyrna rugs, and the patterns were usually of pronounced Baroque or Rococo design. Carpet-making at Axininster began about the middle of the 18th century and continued actively for nearly one hundred years.
Brussels Carpets. In the 18th century Brussels was the leading carpet-producing center in Europe, but in England carpet factories at Axininster and Wilton captured the English market. Brussels carpets are made with the velvet weave uncut, applied to floor coverings. The patterns follow French designs. They are woven usually the width of the Flemish ell (27 inches).
Embroidered Carpets. A name given to a type of carpet of domestic make in this country early in the 19th century. A description of one made by Lucetta Smart of Rumney, New Hampshire, in size 86 by 58 inches, states that it is made of two strips of heavy woolen blanketing sewn together and on this ground the design is worked in a curious kind of chain stitch. The border shows a flowering vine, the field a woven basket from which aris6s a tree, amidst which disport birds. The colors are grey-green, three shades of blue, browns and reds varying in hue. It is quite probable that the so-called embroidered carpet was a forerunner of the hooked rug, a type of floor covering more quickly made, yet durable.
Kidderminster Carpets. Carpet-making was first established at Kidderminster, England, during first half of the 18th century. The product was a two-ply ingrain carpet showing warp and pile on each side, and reversible.
Wilton Carpets. These were first made at Wilton, England, in the 18th century in imitation of the velvet weave of Brussels carpets, but with the loops cut. The English patterns were largely Oriental and average much better than those of Brussels. Of the Wilton products of the 19th century the finest were of lamb's wool only, noted for its luster and long and beautiful fiber. The weaving was done by hand and only vegetable dyes were used.
CARTOON: A study or design executed on strong paper and of the size to be reproduced in tapestry or other weaving.
.CASTOR: Usually describes a hat, either of beaver fur or resembling it.
CHAIN-STITCH: A loop-stitch.
CHENILLE: A silk or worsted cord used in weaving, having short threads set at right angles, forming a velvety thread.
HINA: An English weave of worsted or woolen stuff allied to serge. In Colonial times it was variously spelled "chaney," "cheney" and" cheyney. " Therewas also a reference in old inventories to" cheney satten" and "cheney taffetas ," which may have been of silk.
CHINTZ: A cotton cloth, usually glazed, and printed in various colors. The name was originally applied to the printed cotton cloth from India imported into England in the 17th century. It afterwards was applied to the glazed hand-printed call, coes of European and American manu' facture.
COACH LACE: Not a lace at all, but an ornamental braid used to adorn the interior of coaches. When used in Europe for coach or livery it bore the arms of noble families, or seal of a city if designed for official use, but in this country it was designed on purely ornamental lines and in various colors.
COMFORTER: A bed-covering, usually of cotton and filled between the outer surfaces with loose cotton or wool and knotted at regular intervals to prevent the interlining from slipping out of place.
CORDUROY: A ribbed cotton material.
COTTON: A vegetable fiber, distinguished from all other fibers by the peculiar twist it possesses, which makes it exceedingly valuable for spinning. It is grown under a wider range of climatic conditions, over a greater area, and by a greater number and variety of people, and is useful for a larger number of purposes than any other fiber. Its by-products are also of great importance. The Sea Island and Egyptian long-staple cottons are among the most valuable species. The invention of the cotton gin (q.v.) by Eli Whitney in 1794 gave great impetus to the growing of cotton in this country, by the facility with which the seeds were removed from the boll by the use of that machine. In 1789 the first cotton mill in New England was started at Beverly, Massachusetts.
COTTON CLOTH: Was first produced in England about 1760, and in this country by the beginning of the 19th century it had become an established industry. In Colonial times, cotton was used to some extent for home weaving.
COTTON GIN: A machine for separating cotton fiber from seed, invented by Eli Whitney in 1794. Previously the work had been done by hand, a slow and tedious process. Two types of the gin are now in use-the saw gin of the Whitney type, which does very rapid work and is generally used, and the roller gin, which is much slower but is less likely to injure the fiber. It is preferred for the longstaple cottons.
COTTON PRINTING: In Europe there were crude but ambitious attempts to imitate the cottons of the Orient imported in the 17th century by the East India trading companies. In France the Toile-de Jouy (q.v.) factory, near Versailles, was started in 1760 and work of good quality had been done in other parts of Europe at about the same time. In this country, a few isolated instances of cotton printing are recorded prior to the Revolution but as an industry it dates from the last quarter of the 18th century. At the turn of the century numerous establishments sprang up, particularly in New England and Pennsylvania, and the activities of these manufacturers foreshadowed the development of the enterprise which now occupies so important a part in the economic life of America. In 1803 cottons were first printed by the cylinder process, and rollers were first engraved with the design for calico printing in 1825.
COUNTERPANE: (Or Counterpoint) A bed-covering first mentioned in the Elizabethan period, s&-called from being worked in square or diamond-shaped figures, or panes, derived from the Latin pannus, a piece of cloth. Before the time of Elizabeth it was known as counterpoint.
COVERLETS: (French Couvre-Lit) Embroidered. Made with heavy wool yarn drawn through rather coarse homespun blanketing. They are of late 18thand early 19th-century make. Of these early American embroideries, very few are to be found at the present time. The method used was similar to that later employed in making hooked rugs.
Quilted. These were made on a quilting frame. The earlier ones were usually of linen, but those of the 19th century are of cotton, as a rule. Over the lining was spread a thin layer of cotton or wool and covered with the pieced top. The pattern consisted of single, double or triple lines, diagonal or in squares, diamonds or other design, in fine running stitch, not an extraneous thing but a part of the making. They were frequently adorned with an appliqued design pieced together from bright colored fabrics. Some were quite elaborate in composition. Another method was to lay cords of soft cotton or candle wicking between the top and the lining and quilt them in by a row of stitches on each side. Either method made a most durable and comfortable bed covering. .
Woven. Coverlet weaving was practiced in all of the colonies from New Hampshire to Georgia from early 18th century to the middle of the 19th. They were woven on a hand loom in two strips, usually about thirty inches wide and of the desired length, and then sewed together to make a spread. The warp was usually of white cotton or linen and the woof of colored wool, grown, spun, dyed and woven into the coverlets by the housewife. Blue and red were the favored colors, but yellow, green and brown were also used. These colors were obtained from home-made vegetable dyes and have retained their brilliancy unfaded.
CRETONNE: A French substitute for chintz, heavier, and not in common use until about 1860. It is an unglazed cotton fabric, printed on one side.
CREWEL-WORK: Embroidery in wool on linen. The word is derived from the German Knau2, meaning a ball of wool. This was a type of embroidery that met with great favor in England and the American colonies in the 18th century. Such work was used for curtains, cushions, bedhangings, and for table covers. It continued in popularity until well into the 19th century.
CROCHET: A form of needlework, employing silk, wool or cotton and a hook or needle, and for some years in the 19th century it was the most popular of all of the various forms of fancy needlework.
CROSS-STITCH: Probably the oldest stitch known for use on a woven material, formed by two stitches, crossing at right angles.
CUPBOARD CLOTHS: Used in England and here in Colonial times to cover the tops of cupboards, on which it was customary to display china, pewter or glass. Frequently mentioned in inventories of the 17th century.
CUSHIONS: Cases of woven stuff, leather or needlework, filled with hair, feathers or down.
CUT-WORK: The forerunner of certain lace stitches and used for the decoration of household linens and clothes. It appeared in France as early as the 16th century and it is found on early English embroideries, also.
DAMASK: A rich flat fabric first made in Damascus, which in the 12th century achieved a great reputation for the weaving of splendid patterned stuffs. From there the manufacture spread to Italy and it was introduced into England late in the 16th century. It is a weave with a warp satin ground with a weft satin twill or taffeta pattern, the lines of the figures contrasting sharply with the lines of the ground, causing the shifting sheen as viewed from different angles. Damask was a favorite material for upholstery throughout the 18th century.
DARNICK, DORNECK, DORNICK: A coarse kind of linen fabric used generally for hangings, originally made (17th century) at Dorneck, Dutch name for Tournay. The name was also applied to a coarse variety of checkered table linen.
DENIM: A cotton fabric with a twilled weave on the face side.
DIMITY: A stout cotton or linen cloth used in England in the 17th century, with the name from Latin dimitum, double thread.
DRAPERY: Textile cloths or fabrics used for hangings.
DRESDEN WORK: A combination of lace medallions and embroidery in linen thread or colored silks, made during the 18th century.
DRILL-DRILLING: A fine, heavy, twilled linen or cotton fabric of a satiny finish.
DRUGGET: A coarse cloth of wool or wool mixed with silk used for wearing apparel.
DUCAPE: A stout silk fabric of soft texture, sometimes woven with a stripe. Introduced into England by French refugees in 1685.
DUCK: An untwilled fabric of cotton or linen, not so heavy as canvas, but used for similar purposes.
DUFFEL: A coarse woolen cloth having a thick nap or frieze, originally made at Duffel, near Antwerp in Flanders.
DYEING: The art of dyeing was practiced in some sort by all primitive peoples, the dyes being, derived from vegetable sources. The so-called Tyrian purple was known in the early days of the Roman Empire. It was so expensive that only the very rich could afford it and by the Middle Ages the dye had been lost to commerce. Towards the close of the Middle Ages the art of dyeing was greatly developed in northern Italy, especially at Florence. Subsequently, discoveries of new dyestufFs and the application of improved processes brought dyeing with vegetable colors into general use. It was not until 1856 that the first artificial dyestuff derived from aniline was discovered, since which time first aniline, then other colors from coal-tar have superseded the vegetable dyestuffs. Dyeing may be done in various stages of fabric manufacture, depending upon the material and the purpose for which it is to be used.
DYES: From remote times to the middle of the 19th century, dyes made of vegetable coloring matter were the only dyes available. Indigo made any shade of blue; madder, all reds from pink to rose; the barks of walnut, chestnut and hickory trees gave a brown dye; and black oak and hickory made green; sumac, wild cherry, and goldenrod gave various yellows; scrub oak, black. Logwood and cochineal were also used. Alum was used for "fixing" the colors. The women of colonial times were very skillful in making and using these dyes, and the colors of the fabrics of those early days that are still in existence remain unfaded today.
EMBROIDERY: The art of producing ornamental patterns by needlework on any fabric which can be sewed over. It dates from the earliest times, and arrived in Europe from the nations of the East. The greatest perfection in European embroidery came in medieval times, and the most highly appreciated examples are of English origin. The fabrics principally used in embroidery work are linen, silks, satins, velvets and flannels. The materials employed are colored worsted yarns (crewels), and silk. Some of the principal stitches are the chain or tambour-stitch, the button-hole stitch, the feather-stitch and the Berlin-work stitch. A distinct class of embroidery consists of applique or cut-work, in which designs of different materials and colors are cut out and sewed down on the surface of the fabric to be ornamented. A pattern entirely covering the underlying material, or nearly so, would be described as needlework (q.v.).
ENGLISH TEXTILES: By the end of the 18th century English mechanics by their inventions had revolutionized textile manufacturing and had turned it from a hand industry to one run by power. This gave England great advantages over other manufacturing countries, and the secret of the designs of these new machines was carefully guarded. The earlier inventions of Hargreaves, Crornpton and Arkwright needed but the power loom to make them effective in a large way, and Cartwright provided that in 1785. From that day to the present time Manchester, England, has been a leader in textile production. JACQUARD LOOM: This loom, which has played so important a part in textile weaving since its invention, was perfected by Joseph Marie Jacquard of Lyons, France, about 1806. The Jacquard attachment may be applied to almost any style of loom and it is used in weaving large and complex patterns. One of the earliest used in this country was at the Northrup Woolen Mill at Roanoke, New York, in 1820.
KERSEY: A coarse, smooth-faced narrow wool fabric something like broadcloth but lighter in weight, distinguished by the diagonal ribbed appearance of its upper surface, where the nap, not being raised, allows its structure to be seen. NEEDLEWORK: Needlework is a broad, general term applying to embroidery, lace, and tapestry work. In the Tudor period chairs, upholstered with satin or velvet, were frequently enriched with applied needlework. During the William and Mary and Queen Anne periods in England needlework was particularly devoted to tapestries, in which a coarse canvas ground is entirely covered by close-set stitches of wool or silk. This work was accounted the duty of the women folk in country houses in England. Many examples are today in good state of presservation. The stitch generally used is a diagonal called the tent-stitch. Grospoint and petit-point are terms used also for this work, gros-point crossing two meshes of the canvas, and petit-point, the smaller, crossing but one mesh. In general, the designs follow those for tapestries and other textiles of the periods. Crewel-work was popular, also designs in imitation of the Chinese silks, embroideries, and other textiles imported at that time from the East. Some of the most important needlework panels were those designed for wall-hangings in imitation of woven tapestry. About 1770, needlework covers for seat furniture were superseded by silks, satins and tapestry.
Needlework in the American colonies was largely utilitarian, although as time passed and the conditions became somewhat easier for women, they indulged their taste for decoration and ornamentation by means of their needle. Firescreens, chair seats, bed-coverings and articles of clothing gave evidence of their skill and taste. Samplers, too, afforded work for the younger generation.
NEEDLEWORK PICTURES: In England needlework pictures in imitation of tapestry were made as early as the Tudor period and they were continued until the days of the Stuarts, corresponding roughly with the years during which tapestries were produced. The subjects consisted of Biblical scenes, chiefly, although there were others of current interest. Some of the later pictures were a combination of needlework and paint. The effect of these, in many instances, approaches the grotesque. One of the finest needlework pictures in existence today is to be seen in the Cluny Museum in Paris. It is a panel in high and low relief of the 16th century, representing the story of Eden. It is truly a work of art. In this country these pictures were introduced by the Moravians, who came to Pennsylvania soon after 1700. In their schools, they taught fine white embroidery, tambour, crewel-work, and the making of pictures with a needle on silk and satin. In the late 18th and early 19th centuries, this work became very popular in their district, and went under the name of Moravian-work.
TAPESTRIES: Tapestry-making is weaving, and its principle is simple. Colored threads, usually of wool or silk, constitute the web, and are woven across other threads, generally of linen, which constitute the warp. A tapestry is a pictured cloth with a ribbed or rep surface woven either on a vertical, high-warp (haute lisse) or on a horizontal, low' warp (basse lisse) loom. In the former the warp is vertical and the woof horizontal; in the latter, the woof is vertical and the warp is horizontal. The high' warp tapestry was known to antiquity and in the celebrated periods of weaving in Europe the high-warp loom has been the one in use. The low-warp loom came into use in France about 1600. It is almost impossible to distinguish the difference in the product of the two methods. The weavers of the 18th century put a single red thread along the top and bottom of a tapestry woven on the low loom to distinguish it. All old tapestry, is of course, hand-woven.
From very early times the inhabitants of Western Europe were renowned for their woven fabrics. The weavers at Arras are said to have begun weaving in the 9th century. Weaving was done in monasteries in France far several centuries. In the 13th century the craftsmen organized guilds and from that time tapestry weaving became an established industry. In tapestry there are four important groups; Gothic, 14th and 15th centuries; Renaissance, 16th century; Baroque, 17th century; Rococo and Classic Revival, 18th century. Before the 14th century there were primitive tapestries only.
The art of tapestry-making came to Europe from the East, and in the 14th century at Paris and at Arras in Flanders designers and weavers were able, with a few colors, to manipulate threads into the strongest and liveliest contrasts of form, color and tone that can be achieved on a flat surface. France is the mother of Gothic tapestries, and Arras gained such distinction that its name became the synonym for tapestry of the finest quality. In the last quarter of the 14th century the craft of the tapestry weaver was in the most prosperous condition it knew in France in the Middle Ages. In the next century Brussels and Bruges and Tournai in Flanders took the lead under the influence of designs by Flemish and Italian artists, and by the middle of the 16th century Flemish tapestry attained a degree of perfection which has never since been surpassed. Much of the wool for the finest French and Flemish tapestries was imported from England. In return, the tapestries of Arras and Flanders were sold in England. In Italy, Ferrara, Florence, Milan and Rome were also noted for fine tapestries in that century.
In the 17th century Brussels lost its leadership through haste and excessive production, and the tapestries woven at the Gobelins' (q.v.) factory in Paris, fostered by King Louis XIV, took first place before the end of the century, and in England tapestries were produced at the Mortlake factory, founded in 1619 by Sir Francis Crane, which were of the highest order of merit. The best tapestries of the 18th century were those of Beauvais (q.v.) but the high standards of the early tapestries had degenerated. The difference is mainly of texture, though also caused by the different character of the designs and by the attempt to use too many shades of coloring. Since the 18th century no really great tapestries have been made.
Gothic and 18th-century tapestries have narrow borders or none; Renaissance and Baroque tapestries have wide borders, some of them of great beauty. Gothic tapestries excel in reds; Renaissance in whites and golden yellow; Baroque in blues; Rococo in rose; while Classic Revival colors are weak and pale. The most important distinguishing feature of old tapestries is the open slits which separate the different parts of the design, different in this respect from damasks, brocades and other weaves. In the prominent museums in this country and in Europe, and in some private collections too, there are to be seen many of those early masterpieces of woven art. A great many have been destroyed by the ravages of time and by the wilful purpose of man, especially in France during the time of the French Revolution. Those tapestries that survive well deserve the care and admiration now bestowed upon them.
American Tapestries. The first tapestry produced in America was woven on a small loom in New York in 1893 by a Frenchman. Since that time other looms of the low-warp pattern have been set up, workmen obtained from abroad, and some creditable copies of old tapestries have been made.
Aubusson Tapestries. Weaving of tapestry was established here before the 17th century, and as early as 1637 had more than two thousand workers on low-warp looms. The industry was greatly injured by the Revocation of the Edict of Nantes in 1685 and by the hard times that prevailed in France in the last decade of the 17th century. In 1731, the French Government assisted by sending a dyer and a designer from the Gobelin factory; prosperity began anew, and the best period of tapestry weaving in Aubusson is from 1740 to 1790. Distinguishing features of the early product are the dazzling whites and the loose texture..
Beauvais Tapestries. This famous factory was founded in 1664. It was a step in the campaign that transferred the tapestry supremacy from Flanders to France. The factory here produced tapestries for the general public, while the Gobelin factory was devoted to work for state purposes. Compared with those made at Gobelins' the Beauvais tapestries were inexpensive. In the 18th century, largely because of the designs of the artist Boucher, the work of Beauvais is comparable with the best tapestries of the earlier centuries.
English Tapestries. The first English factory of any continuity appears to have been the Sheldon Looms, established at Barchester in Warwickshire by William Sheldon about the middle of the 16th century. The tapestries produced there compare favorably with the finest contemporary Flemish weavings. Some of these consisted of large tapestry maps of English counties. The great name in the history of tapestry-making in England is Mortlake in Surrey County in the 17th century. From 1620 to 1636 these tapestries, made under Sir Francis Crane by expert weavers from Flanders, rival those of the later Gobelins and surpass those of Brussels of the period. Sir Francis Crane died in 1636 and the establishment became known as "The King's Works." The factory lost royal support in the troubled times of the reign of Charles I and, after struggling through the times of the Commonwealth and the Restoration, finally passed out of existence in the reign of Queen Anne. There were also some other minor factories in England during this period, and one in Ireland. Several are of record during the 18th century, Lambeth, Fulham and Soho.
Gobelin Tapestries. The history of Gobelins begins with the establishment on the banks of the Bievre river in Paris of a dye factory, by Jean and Philibert Gobelin, brothers, at the end of the 15th century. In the following century they added to their dyework a tapestry manufactory. In 1662, the factory attracted the attention of Colbert, French finance minister, who purchased the works, and in 1664 the King, Louis XIV, established it as a royal manufactory under the direction of Charles Le Brun, the great master of decorative art of that period, who with a great number of artists and artisans brought the production of tapestry to a high state of perfection in design and weave. From that time the Gobelins have been the most artistic tapestries anywhere produced. The finest set was the History of the King (Louis XIV), a grand historical document. The set numbered fourteen hangings. The History of Alexander in eleven hangings is another famous set. During the 18th century the Gobelin tapestries failed to reach the high standards of the earlier work. The Savonnerie (q.v.), an establishment founded by Henry IV for velvet pile carpets and hangings, was combined with Gobelins' in
Rhenish Tapestries. Along the banks of the Rhine from Basle to Mayence, there existed through the entire 15th century a flourishing industry of tapestry weaving. The production was small, the work was quite individual, and in type different from the Flemish tapestries df the same period.
Russian Tapestries. Peter the Great established the Imperial Tapestry Factory at St. Petersburg in 1716 with French weavers from Beauvais. Some notable tapestries were made there but the factory was discontinued in 1859. Spanish Tapestries. The Royal Tapestry Factory was established in Madrid in 1720 and is still in operation. The best were those woven in the last quarter of the 18th century from designs by Goya.
TAPESTRY FURNITURE COVERING As furniture became much more diversified in the 18th century, tapestry coverings became common. France set the example and most of these coverings were made at Beauvais on low-warp looms and at the Gobelin works. Aubusson also produced many attractive sets. Tapestry coverings all in silk are much inferior to those that have the proper proportion of wool.
TEXTILE PRINTING: In printing fabrics the color is stamped on from an engraved block or roller. The process, in one form or another, can be traced back to remote times. In the 17th century the industry was revived, and in 1676 textile printing was introduced into England by a French refugee who opened an establishment on the Thames River near Richmond. In the last half of the 18th century the art was brought to a high state of perfection in France, especially at the Toile-de Jouy factory (q.v.) of Oberkampf. The first factory for printing fabrics in America was started in 1774 at Kensington, near Philadelphia, by John Hewson, an Englishman who had gained his knowledge of the business in England. Although the industry grew rapidly in this country American prints have never quite reached parity with those from abroad. At the end of the 18th century metal rollers took the place of wooden blocks and the modern machine period had begun. The printing of woolen and silk cloths is similar to that of cotton or linen except that the woolen cloth requires more preparation and the silk cloth less.
TIFFANY: The term for transparent silk, gauze muslin or cobweb lawn, 17th century.
TOILE-DE JOUY: French chintz manufactured at Jouyen Josas in the Bievre valley near Paris, in a factory established in 1760 by Christophe-PhilippeOberkampf (17381815). The chintzes were printed with designs by master artists of the period, of whom Jean Baptiste Huet from 1773 to 1811 was the most prominent, and they became very popular in France, and later in England. Colors used were sepia, mauve, blue, grey, green, black and madder red. After the death of Oberkampf the factory gradually dwindled in importance and in 1843 it was torn down.
TOILINETTE: A cloth for waistcoats with weft of woolen yarn and warp of cotton and silk. Name from the French toilinet, in turn from toile, a canvas.
Tow The short fibers of flax made into a heavy thread, used for burlaps and coarse clothing stuff, and, when woven, called tow cloth.
TURKEY-WORK: A home product of Colonial times in this country, also imported from England, made in imitation of Oriental pile rugs by threading woolen yarns through a coarse cloth of open texture (canvas or burlap) then knotting and cutting the ends. It became very popular for chair coverings and table and cupboard cloths.
UPHOLSTERY: The earliest forms of upholstering in England were state canopies and beds. A diversity of material was employed, plain and embroidered velvet, satin, tapestry, needlework, and even leather was used. Later, chintz and Indian calicoes came into favor. In the 17th century, fringes became an important feature of upholstery and continued in use until the end of the 18th century. Metal fringes and tasseled silk floss fringes were introduced from France and Italy during the Restoration and afterwards copied in England. Allusions to upholstery are numerous in the 18th century in all of the cabinet-makers' books of the period, and the upholsters' trade reached its zenith at that time. In this country, chair seats were covered early and by the end of the 17th century upholstered furniture was comparatively common. During the 18th century the use of upholstery in general paralleled its use in England.
VALANCE: A hanging drapery for beds, windows, etc.
VELVET: (French, Velours) A silk fabric with a short, close, soft nap. It is believed that the first velvet was made in China, but the early centers of velvet-making in Europe were the cities of Lucca, Genoa and Florence in Italy. Later Venetian velvets became noted, and the art was taken up in the Low Countries. After the Revocation of the Edict of Nantes, French silk weavers migrated to England, and plain and figured velvets were made at Spitalfields, though not equal to Italian velvets. Velvets were then much used for hangings, but in the 18th century velvet lost favor, being replaced by lighter fabrics. A cheaper product known as Utrecht-velvet, consisting of worsted mohair, or of mohair and cotton, was also used for upholstery and hangings. The pile of modern velvets is produced by extra warps that loop over wires, which are withdrawn after the passage of the binding weft. So-called velvet carpets such as Wilton (q.v.) are made by the use of the velvet weave applied to floor coverings of wool.
WEAVING: Weaving is the art of making cloth on a loom (q.v.). There are three fundamental weaves-plain, twill and satin. Others, such as taffeta, damasks, brocades and velvets are merely variations or complications of these three. For many centuries weaving was carried on as a household industry with little or no change in the style of the loom or in the methods employed, and though the loom was remarkably simple, even crude, the operators produced fabrics that have never been excelled in fineness of texture, even at this later day. The materials in early use in this country for weaving were wool, flax and hemp. Cotton came later. The periods just before and following the Revolutionary War are considered the high spots in American home-weaving. It was not until the latter half of the 19th century that all of the processes connected with weaving were grouped together in one establishment, the mill.
WOOL: Next to cotton, wool is the most extensively used of all fibers. A pound of the finest wool will yield nearly 100 miles of thread. Although the typical wool is produced by sheep, goat's hair furnishes a long, fine silky material, much used in making beautiful textile fabrics. The angora goat yields mohair, the alpaca goat a fiber known as alpaca, and the wool made from the cashmere (kashmir) goat of India is said to be the most costly of all wools. The fine soft hair of the camel approximates sheep's wool in its structure. The wool grown in this country was much improved in quality early in the 19th century by importation of large numbers of merino sheep from Spain, where cross-breeding had been carried on scientifically for generations.
|
|
|